Our Blog
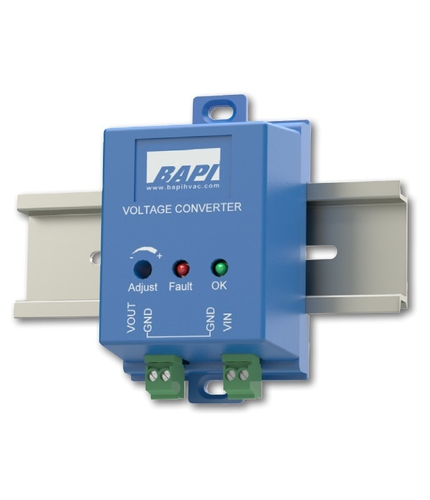
Voltage Converters: Learn How They Work and How to Pick the Best Type
Have you ever tried plugging in your phone or hair dryer overseas, only to fry it within seconds? A voltage converter can save your day in this case. Whether you’re charging gadgets, powering appliances, or switching between voltage systems, having a voltage converter is very important.
With the standard nominal voltage of 230 volts common in Australia, travelling with or importing devices often comes with voltage mismatches. In this article, Controls Traders explains how converters work, what to look for, and how to pick the right one for your needs.
What is a Voltage Converter?
A voltage converter, also called a power converter, is an electricity management appliance that changes electrical voltage into compatible voltage levels for devices. It ensures your appliances get the right amount of power, no matter where you are.
We have various forms of voltage converters, from step-up converters, which increase the input voltage, to step-down transformers, which decrease it.
How Does a Voltage Converter Work?
A voltage converter works by stepping up or down to match your device’s needs. It’s like a translator for electricity, ensuring smooth power flow. HVAC systems use specific power supplies, for instance. A power converter ensures compatibility, especially in global installations.
Electrical devices work with specific voltages. When you plug a 230V device into a 120V socket, there’s not enough power to run the appliance.
Types of Voltage Converters: AC to DC, DC to DC, and More
Voltage converters come in different types. We'll break each down below:
1. AC to DC Converter (Rectifier)
An AC-to-DC converter transforms alternating current into direct current by allowing the flow of current in just one direction. It essentially "straightens" the current flow, working like a one-way valve for electricity.
Low-power devices like cell phones and laptops need DC electricity to run. But most outlets provide AC. The AC to DC voltage converter, or rectifier, converts AC from your wall socket to the DC your gadgets need.
In Australia, these converters are everywhere—from power banks to phone chargers. They’re a must-have if you’re travelling multiple countries with gear that relies on DC power.
2. DC to AC Converter (Inverter)
A DC to AC voltage converter takes DC power (from car batteries, solar panels, to power banks) and turns it into AC.
If you’re off-grid with only a solar panel, an inverter lets you use regular appliances like laptops, dryers, or even a small coffee machine. For HVAC professionals, inverters are needed while working with off-grid or renewable power setups.
3. AC to AC Frequency Converter (Transformer)
Australia runs on 50Hz electricity while the US uses 60Hz. You'll need a frequency converter or transformer if you’re using appliances or tools made for a different frequency.
For example, an imported HVAC unit may require a transformer to handle Australia’s power. It’s not just about voltage but also frequency compatibility.
4. DC to DC Voltage Converter (Current Converter)
A DC-to-DC power converter adjusts voltage levels between DC-powered devices.
For instance, powering multiple devices from a car battery, like GPS, dash cams, and phones, requires converting voltage down to match each device. Without it, you may damage your gear.
Choosing the right voltage converter is essential. At Controls Traders, we stock everything from rectifiers to transformers.
Voltage Converter vs. Adapter: What's the Difference?
Adapters are like translators. They don’t change electricity, just the plug shape. For example, Australian outlets use a three-pronged plug. If your device is from the US, you’ll need a travel adapter to make it fit. But beware: travel adapters don’t adjust voltage.
Voltage converters, on the other hand, change the voltage to protect single-voltage devices like hair dryers or some power tools. Australia typically runs on 230 volts, but US appliances often run on 110 volts. Without a converter, that mismatch can fry your device.
What to Look for When Buying a Voltage Converter
The right power converter can save your gear from costly damages. Here are what to consider:
1. Wattage Capacity
Start here. Check your device’s wattage needs. Hair dryers, for example, require up to 2000W. If your converter can’t handle it, you’ll be left with a fried appliance or no power at all.
2. Dual Voltage Compatibility
If you’re running both low-power devices like toothbrushes and larger appliances, a dual voltage converter is what you need. It works with multiple devices at home and abroad.
3. Compact and Lightweight Design
Would you like to travel light? Then choose a converter that won’t weigh down your luggage. Compact units are perfect for globetrotters, whether you’re backpacking through Europe or jetting to Japan.
4. Surge Protection
Power surges happen. Protect your gear with a converter that has a built-in surge protection. It’s a must for sensitive gadgets like laptops, tablets, and phones.
5. Global Plug Compatibility
Planning trips to the USA, China, or Switzerland? A converter with multiple plug adapters helps you stay powered wherever you go.
Controls Traders is here to help. We stock reliable converters, power supplies, and HVAC products designed to meet Australian standards. Browse our range today and power your life. Or call us if you have any enquiries.
Frequently Asked Questions
Do I need a voltage converter or just an adapter?
Use an adapter when your device is dual-voltage (check the power details on the label). Most modern gadgets, such as laptops, phones, and power banks, work with multiple voltages; they just need the right plug to fit the socket.
Use a power converter if your device is single-voltage (look for a number like "110V").
What is a voltage converter used for?
A voltage converter changes the voltage of electricity to suit your devices. For example, if you bring a 110V appliance from the US to Australia (which uses up to 240V), you'll need a converter to protect your device from getting fried. It’s essential for single-voltage gadgets.
Can a power converter work for multiple devices at once?
Yes, but check the wattage of all the devices you plug in so you don't overload the converter. When trying to plug in your laptop, phone, and hair dryer at once, do the math. Overloading your converter could damage it—or, worse, your appliances.
Do I need a voltage converter for Australia?
That depends on your device. If it’s dual-voltage (e.g., 110-240V), you can use an adapter. However, check the label on your device. If it only says "110V" or "120V," get a converter.
How do I check if my device is dual voltage?
Flip your device over and read the label. Look for something like "Input: 110-240V." This means your device can handle multiple voltages without a converter. However, you'll need a converter for single-voltage items like certain kitchen appliances or power tools.
Check out our range of voltage converters or contact us for further guidance on choosing a converter.
Read more
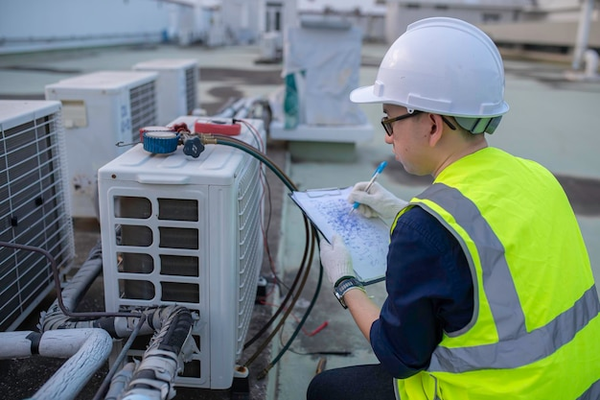
What is a Variable Speed Drive? A Beginner’s Guide to Understanding VSDs
A Variable Speed Drive (VSD) is a vital tool for optimising the operation of electric motors across a wide range of industrial applications. These systems deliver precise speed control, ensuring electric motors run at their most efficient speed to meet specific load requirements. By enabling advanced motor control, variable speed drives reduce energy consumption, extend the life of mechanical equipment, and minimise operating costs.
Whether you're exploring what is a variable speed drive or looking to enhance energy efficiency, understanding the role of variable frequency drives (VFDs) is crucial for optimising operations.
What is a Variable Speed Drive?
A Variable Speed Drive is an electronic device that regulates the motor's speed by modifying the input voltage and frequency supplied to the motor. This ability to tailor motor performance ensures efficient operation at full speed, reduced speeds, or anywhere in between.
How Does a Variable Speed Drive Work?
Variable frequency drives adjust the output voltage and frequency, enabling motors to meet changing demands without unnecessary energy use. Components like pulse width modulation (PWM) and voltage source inverters are key in achieving this accurate control.
For instance, in pump and fan applications, a variable speed drive pump reduces waste by ensuring the motor load matches the system's requirements, delivering optimal energy savings.
Why Use Variable Speed Drives?
Addressing Fixed Speed Challenges
Traditional motors operate at a constant speed, consuming the same amount of energy regardless of the task's actual demands. This often leads to unnecessary electricity consumption and higher energy costs.
The Benefits of Speed Adjustment
A variable frequency drive (VFD) enables motors to adjust their speed based on the load, delivering:
- Significant energy savings.
- Reduced mechanical stress and wear on components.
- Enhanced flexibility for systems where the system requires frequent braking or variable loads.
By installing variable speed drives, industries can achieve greater efficiency and reduce electricity consumption across operations.
Types of Variable Speed Drives
Choosing the right speed drive is essential to meet specific operational needs. Several types of variable speed drives are designed to support various industrial applications.
AC Drives
AC drives are used with ac motors, including ac induction motors and synchronous motors. These drives adjust the output frequency and input voltage, making them ideal for applications requiring continuous operation, such as HVAC systems and manufacturing lines.
DC Drives
A dc motor variable speed drive is suitable for tasks requiring constant torque, such as conveyor belts or other heavy machinery. By regulating the dc voltage, these drives ensure reliable and efficient motor control.
Adjustable Frequency Drives
Also called variable frequency drives, these devices are versatile, capable of handling both light and heavy loads. They optimise electric motors in pump and fan applications, using power electronics to achieve precise speed control and reduce electricity consumption.
Benefits of Using Variable Speed Drives
Energy Efficiency
Variable speed drives dynamically adjust the motor's speed to match demand, significantly reducing energy consumption. This capability is particularly valuable in systems with fluctuating loads.
Cost Savings
Lower electricity consumption leads to reduced operating costs, helping industries save money while maintaining optimal performance.
Extended Equipment Lifespan
By minimising mechanical stress and electrical stress, variable speed drives prolong the life of mechanical equipment, reducing maintenance needs and downtime.
How Variable Speed Drive Motor Works in Industrial Settings
Practical Applications of VSDs
Variable speed drives are used in a range of industries to improve efficiency:
- HVAC Systems: AC drives manage airflow by controlling ac motors, ensuring energy-efficient heating and cooling.
- Manufacturing Lines: Synchronised motor controllers maintain seamless operations with precise speed control.
- Renewable Energy Systems: Medium voltage AC drives stabilise output in wind and solar power plants, minimising energy fluctuations.
Components of a Variable Speed Drive
- Voltage Source Inverter: Converts power to the required output voltage and frequency.
- Pulse Width Modulation (PWM): Provides fine-tuned motor speed control.
- Dynamic Braking: Ensures safe deceleration in systems where the system requires frequent braking.
By managing input voltage and output frequency, variable speed drives enhance the efficiency of electric motors, even in challenging conditions.
Selecting the Right Variable Speed Drive
When choosing a variable speed drive, assess the following:
- Motor Type: Ensure compatibility with your ac motor or dc motor.
- Application Needs: Determine if the drive supports pump and fan applications or heavy-duty mechanical loads.
- Energy Savings Goals: Use tools to estimate energy savings and prioritise
Future of Variable Speed Drives
The next generation of variable speed drives focuses on sustainability and automation. Key advancements include:
- IoT Integration: Enables real-time tracking of motor load, operating speed, and energy use.
- AI-Driven Systems: Automatically optimise performance for maximum energy efficiency.
- Eco-Friendly Designs: Incorporate renewable energy solutions to minimise the carbon footprint.
Conclusion
Optimise your energy efficiency and reduce costs with the right variable speed drive. At Controls Traders, we provide expert advice to help you select the best solution for your specific industrial applications, whether you’re managing pump and fan applications, manufacturing systems, or renewable energy systems.
Visit Controls Traders for expert advice and tailored solutions to enhance your industrial systems.
Frequently Asked Questions
What is a Variable Speed Drive and why is it used?
A Variable Speed Drive adjusts motor speed to reduce energy consumption and optimise efficiency in industrial applications.
How do Variable Speed Drives save energy in industrial applications?
They match the motor’s speed to the required load, ensuring operations are performed at the most efficient speed.
What are the differences between AC and DC Variable Speed Drives?
AC drives control ac motors with variable loads, while DC drives provide steady torque for dc motors.
What should I consider when selecting a Variable Speed Drive for my facility?
Focus on compatibility with the motor type, specific application needs, and potential energy savings.
What are the common issues faced when using a Variable Speed Drive and how can they be resolved?
Common problems, such as overheating, are often due to incorrect settings. Regular maintenance resolves these issues.
Read more
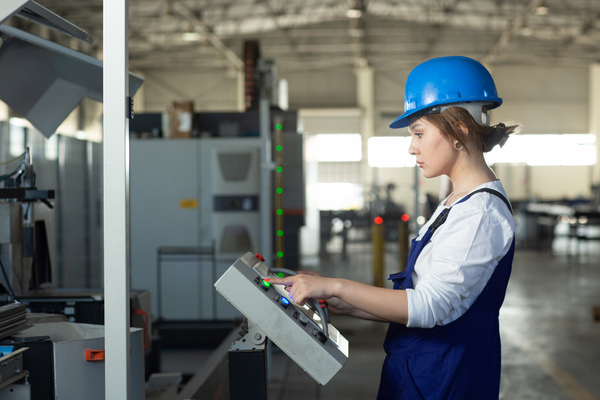
What is a VFD in HVAC and How Does it Work?
Have you ever noticed how your air conditioner blasts cold air at full-speed, even when it’s only mildly warm? That’s energy down the drain. Now, imagine if it could adjust itself, slowing down when needed, speeding up when necessary. That’s exactly what a Variable Frequency Drive (VFD) does in an HVAC system.
A VFD is a motor controller that regulates the speed of an electric motor by varying its frequency and voltage. Instead of running at full speed all the time, the motors only work as hard as they need to. That means lower energy consumption, less wear and tear, and better system performance. Let’s unpack it a bit more.
VFD Meaning: What Does VFD Stand For?
VFD stands for Variable Frequency Drive. It’s sometimes called an AC drive or adjustable speed drive, but the idea is the same. It controls how fast a motor spins.
So, how does it do that? A VFD tweaks both the frequency and voltage of the electricity going to a motor. The lower the frequency, the slower the motor. The higher it is, the faster it runs.
Now, you might’ve heard of a Variable Speed Drive (VSD) and wondered, “Isn’t that the same thing?” Not quite. A VSD refers to any device that changes a motor’s speed, while a VFD specifically does it by adjusting frequency and voltage.
Think of it like this—every VFD is a VSD, but not every VSD is a VFD. It’s like how all squares are rectangles, but not all rectangles are squares.
Now, let’s go into how a VFD actually works.
How Does a VFD Work in HVAC?
Controlling Motor Speed with Frequency and Voltage
Have you ever left a tap running full blast when you only needed a trickle? That’s what happens when an HVAC system runs at full speed all the time. It wastes energy.
A Variable Frequency Drive (VFD) fixes this by adjusting motor speed to what's needed. It changes the frequency and voltage of the electricity supplied to the electric motor, letting it speed up or slow down as needed.
When demand is low, the motor slows down, using less power. When more airflow or cooling is needed, it speeds up. This speed control cuts energy consumption, improves efficiency, and reduces wear on equipment. In fact, HVAC systems with VFDs can slash energy use by up to 50%, which is great for both the environment and your power bill.
Key Components of a Variable Frequency Drive (VFD)
A VFD isn’t just a black box that magically saves energy. It has four key parts working together to control motor speed:
- Rectifier: Converts AC power into DC voltage.
- DC Bus: Stores and smooths the DC voltage, ensuring steady power.
- Inverter: Converts DC back to AC using pulse width modulation (PWM), controlling the output voltage.
- Control Unit: The brains of the operation. It adjusts the frequency and voltage, managing motor speed and response.
Together, these components make sure the electric motor runs only as hard as it needs to—no more, no less.
Why Use a Variable Frequency Drive (VFD) in HVAC Systems?
Think about an office building on a mild spring day. The aircon doesn’t need to work as hard, but without a VFD, it still runs like it’s the middle of summer, which is wasteful, right?
With a variable frequency drive, the system slows down when cooling demand drops and ramps up when needed. That means better efficiency, lower costs, and longer-lasting equipment.
Energy Savings and Efficiency
HVAC systems consume a massive chunk of a building’s electricity, up to 70% in some cases. Running them at full speed all day is like driving a car with your foot flat on the accelerator, even when you're in traffic.
A variable frequency drive (VFD) solves this by adjusting motor speed to match demand. Less power wasted means lower energy bills. In commercial buildings, VFDs can cut electricity costs by 30% to 50%, which adds up fast.
Reducing Equipment Wear and Enhancing Performance
Have you ever heard an old aircon unit rattle and shake when it kicks on? That’s the strain of starting at full power. It wears down components and leads to breakdowns.
With a VFD, motors start up gradually, reducing stress on motor windings and driven equipment. That means less maintenance, fewer breakdowns, and a longer lifespan for HVAC systems.
It’s simple: less strain, fewer repairs, more savings. That’s why we recommend that VFDs be used in modern HVAC systems.
Choosing the Right Variable Speed Drive (VSD) for HVAC
Picking the right variable speed drive (VSD) for your HVAC system isn’t just about power. It’s about efficiency, longevity, and cost savings. Get it wrong, and you could be dealing with overheating motors, higher energy bills, or unnecessary breakdowns. So, how do you choose the best one?
Sizing and Selection Guide for Variable Frequency Drives
Size matters, especially with variable frequency drives (VFDs). Choose wrong, and you’re either overloading your system or wasting money on an oversized unit. Here’s what to consider:
- Motor Power: Your VFD must match the motor load. Check kW ratings and ensure the drive isn’t underpowered.
- Voltage Levels: In Australia, HVAC motors typically run at 230V single-phase or 415V three-phase. So, get a VFD with the right input and output voltage.
- Load Type: HVAC systems usually require a variable torque drive. That means your VFD needs a capacity to control ramp speeds efficiently.
For example, in a commercial building, a VFD running an AC induction motor might need pulse width modulation (PWM) for smoother operation. No one wants a jerky airflow system.
Installation and Maintenance Best Practices
Installing a variable frequency drive VFD is not rocket science, but get it wrong, and you’ll be calling an electrician more often than you’d like.
Here’s how to get it right:
- Proper Wiring: Connect it correctly to the power supply and motor windings. Use shielded cables to avoid interference.
- Cooling & Ventilation: VFDs generate heat. Keep them in a well-ventilated space to prevent overheating.
- Routine Checks: Dust and debris can clog vents. A quick monthly clean helps save energy and improve lifespan.
- Monitor Performance: Use built-in diagnostics to fine-tune system performance. Adjusting motor speed can slash power costs.
Note: A well-maintained variable frequency drive can last 10+ years, keeping your HVAC system running efficiently.
Best HVAC Variable Frequency Drive (VFD) Brands
Not all VFDs are the same. Some last longer, run smoother, and offer better energy savings. Here are the top brands trusted in Australia:
- Siemens: Siemens is known for energy savings and intelligent motor control. Great for large-scale HVAC systems.
- Danfoss: Danfoss is the leader in HVAC VFDs. Their VLT and Vacon drives are found in many Aussie buildings.
- ABB: Reliable and built for medium voltage AC drives. Ideal for high-performance applications.
- Schneider Electric: Easy to use, with built-in protection against power surges. A solid mid-range option.
Need a reliable VFD or AC drive for your HVAC system? Check out Controls Traders in Adelaide. We stock high-quality drives from Danfoss to Siemens and more.
Final Thoughts
A variable frequency drive does more than just control motor speed. It reduces energy consumption, extends motor life, and keeps your HVAC system running smoothly.
Choosing the right VFD means fewer breakdowns, lower power bills, and a more comfortable space. So whether you’re managing an office, shopping centre, or industrial plant, a well-sized variable speed drive is a smart investment.
Need help finding the best VFD? You can shop for them here at Controls Traders on our dedicated store for variable speed drives.
Frequently Asked Questions
What are the three types of VFD?
There are three main types of variable frequency drives (VFDs)—Voltage Source Inverter (VSI), Current Source Inverter (CSI), and Pulse Width Modulation (PWM). VSI is the most common and works well for HVAC systems. CSI is used in heavy-duty industrial settings, while PWM provides the smoothest speed control, reducing noise and making motors run more efficiently.
What is the difference between a PLC and a VFD?
A Programmable Logic Controller (PLC) is like the brains of an operation, while a VFD is the muscle. A PLC manages different system processes, like turning fans on and off or adjusting airflow. A VFD is a type of AC drive that controls the speed of the motor, making sure it runs at just the right level instead of wasting energy.
Is a VFD used in AC or DC?
A VFD is made for AC motors, especially AC induction motors. It takes incoming AC power, converts it to DC voltage, then turns it back into AC power at different frequency and voltage levels. This lets the system fine-tune motor speed, helping save energy and extend the life of the equipment.
What is the difference between an inverter and a VFD?
An inverter changes DC power into AC power, like what you’d see in solar or backup battery systems. A VFD, on the other hand, is a type of motor controller that drives an electric motor by tweaking frequency and voltage. This means a VFD doesn’t just convert power—it actively controls how fast a motor runs, making it perfect for HVAC and industrial systems.
How do frequency and voltage affect motor speed in a VFD system?
In a VFD system, frequency and voltage work together to set the speed of the motor. More frequency and voltage means faster speed. Less means slower. This speed control is what makes variable frequency drives so useful—they adjust power based on demand, cutting down on energy consumption and preventing unnecessary wear and tear.
Got more questions or need help choosing a VFD? Send us a message or call us at 1300 740 140
Read more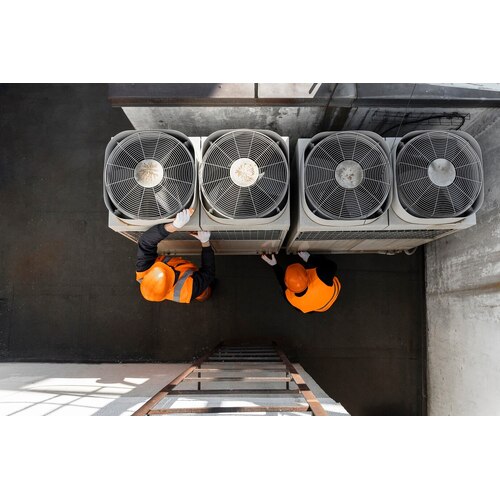
Common Symptoms of a Faulty Suction Control Valve
The Suction Control Valve (SCV) is a crucial component in HVAC systems, regulating refrigerant flow and pressure to maintain optimal performance. It ensures precise control of refrigerant circulation, preventing over- or under-supply that can affect efficiency. A malfunctioning SCV can lead to inconsistent airflow, reduced cooling or heating capacity, and increased energy consumption.
What Is a Suction Control Valve?
A suction control valve regulates refrigerant flow and pressure in an HVAC system. Located within the compressor, it adjusts suction levels to maintain optimal system performance.
Key benefits of a well-functioning SCV include:
- Precise Refrigerant Flow: Ensures the right amount of refrigerant circulates for efficient cooling or heating.
- Optimised Performance: Maintains system efficiency by preventing over- or under-supply of refrigerant.
- System Protection: Reduces strain on the compressor, extending the lifespan of HVAC components.
Suction Control Valve Symptoms
Identifying suction control valve issues early can prevent costly HVAC system failures. Common signs include:
- Irregular Airflow: Fluctuating air distribution due to inconsistent pressure regulation.
- System Short Cycling: Frequent on-and-off cycling caused by improper refrigerant flow.
- Higher Energy Consumption: Increased power usage due to inefficient system operation.
- Unexpected Shutdowns: Sudden system failure linked to pressure imbalances.
- Reduced Cooling or Heating Efficiency: Limited performance as the system compensates for valve malfunctions.
Identifying suction control valve issues early can prevent costly HVAC failures. Common signs include irregular airflow, frequent short cycling, higher energy consumption, unexpected shutdowns, and reduced cooling or heating efficiency. Addressing these issues promptly helps maintain optimal system performance.
Root Causes of Suction Control Valve Failures
Suction control valve failures in HVAC systems often result from:
- Wear and Tear: Continuous operation leads to gradual deterioration, reducing efficiency over time.
- Contaminated Refrigerant: Moisture, debris, or impurities in the refrigerant can clog or damage the valve.
- Electrical Issues: Faulty wiring, damaged connectors, or irregular voltage supply can cause erratic valve performance.
- Poor Maintenance: Lack of regular inspections and servicing allows minor issues to worsen, leading to system inefficiencies or failures.
How to Test a Suction Control Valve
To test a suction control valve, follow these steps:
- Inspect the SCV:
- Check for visible damage or debris on the valve.
- Use a Diagnostic Tool:
- Scan the ECU for fault codes that indicate a malfunctioning SCV.
- Measure Resistance:
- Use a multimeter to test the SCV's connector and confirm it meets standard specifications.
- Pressure Test:
- Monitor fuel rail pressure while the engine runs to check if the SCV adjusts the flow correctly.
Maintenance Tips for Suction Control Valves
Suction control valve failures in HVAC systems often result from:
- Wear and Tear: Continuous operation leads to gradual deterioration, reducing efficiency over time.
- Contaminated Refrigerant: Moisture, debris, or impurities in the refrigerant can clog or damage the valve.
- Electrical Issues: Faulty wiring, damaged connectors, or irregular voltage supply can cause erratic valve performance.
- Poor Maintenance: Lack of regular inspections and servicing allows minor issues to worsen, leading to system inefficiencies or failures.
A new SCV installed with these precautions ensures reliable fuel pump operations and optimal engine performance.
When to Seek Professional Help
Consult a professional if you notice persistent suction control valve symptoms such as rough idling or poor acceleration on your HVAC.
Conclusion
Regular maintenance, using high-quality refrigerant, and monitoring suction control valves are essential for optimal HVAC system performance. Addressing issues early helps prevent costly repairs and system failures. Persistent symptoms should be diagnosed by an HVAC professional, with replacement considered if necessary.
If you’re experiencing suction control valve issues or need a reliable replacement, explore high-quality SCV options and expert assistance at Controls Traders. Keep your HVAC system running efficiently with trusted solutions tailored to your needs.
Frequently Asked Questions
What are the most common symptoms of a faulty suction control valve?
A faulty suction control valve in an HVAC system can cause inconsistent airflow, frequent short cycling, higher energy consumption, unexpected shutdowns, and reduced cooling or heating efficiency. If these issues persist, professional inspection and possible replacement may be needed.
How can I test my suction control valve?
To test your suction control valve in an HVAC system, monitor pressure readings for irregularities, listen for unusual noises, and check for inconsistent airflow. If issues persist, a professional technician can perform diagnostic tests and calibrate or replace the valve if necessary.
What causes a suction control valve to fail?
A suction control valve in an HVAC system can fail due to wear and tear, refrigerant contamination, electrical issues, or lack of regular maintenance. These factors can lead to improper refrigerant flow, reduced efficiency, and system malfunctions.
Is it possible to repair a suction control valve, or should it be replaced?
A suction control valve in an HVAC system is typically replaced rather than repaired as internal components wear out or become contaminated over time. If the valve is malfunctioning, a professional technician can assess whether cleaning or calibration is possible, but replacement is often the most effective solution.
When should I seek professional help for a faulty suction control valve?
A suction control valve in an HVAC system is usually replaced rather than repaired, as wear, contamination, or electrical issues can affect its performance. Seek professional help if you notice inconsistent airflow, short cycling, high energy consumption, or system shutdowns to prevent further damage.
Read more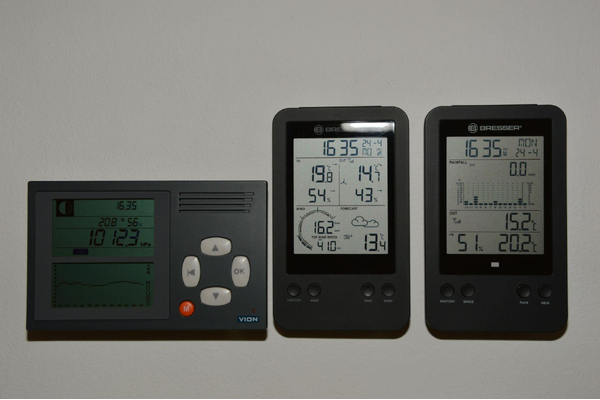
What Is Remote Temperature Monitoring? A Beginner’s Guide
Remote temperature monitoring is the use of wireless temperature sensors and advanced systems to monitor and track temperature in real-time. These systems are vital in temperature-sensitive environments, such as industrial facilities, healthcare, and logistics. They improve operational efficiency by ensuring temperatures remain within preset thresholds, protecting equipment, stock, and ensuring regulatory compliance.
To explore advanced remote monitoring solutions, you can visit Controls Traders, a trusted resource for tailored monitoring systems. By integrating temperature sensors with modern technology like IoT, businesses can easily start monitoring environments, receiving real-time alerts when temperatures rise beyond safe levels.
How Remote Temperature Monitoring Works
The process of remote temperature monitoring involves several components working together:
- Temperature Sensors: Devices that measure temperature and sometimes humidity, ensuring accuracy across a wide range. For example, wireless temperature sensors are used in server rooms and industrial setups.
- Data Transmission: Systems use Wi-Fi, cellular networks, or wireless technology to send data to centralised monitoring software.
- Monitoring Systems: Platforms analyse temperatures in real-time, trigger alarms, and send alerts when conditions deviate from preset thresholds.
By using wireless temperature monitoring systems, industries can efficiently monitor temperature-sensitive environments like storage units, production facilities, and server rooms.
Benefits of Remote Temperature Monitoring
Enhanced Safety
Remote temperature monitoring systems help maintain safe operating conditions by ensuring temperatures don’t exceed critical levels, protecting equipment and devices in various applications.
Cost Savings
These systems help save energy by optimising cooling or heating systems and preventing expensive equipment failures in temperature-sensitive environments.
Operational Efficiency
Through real-time alerts, businesses can quickly respond to anomalies, preventing downtime and ensuring compliance with industry regulations.
Versatility
With temperature monitors, industries can manage a wide range of applications, from protecting stock in logistics to maintaining optimal conditions in server rooms.
Use Cases in Industrial Settings
Manufacturing
Wireless temperature sensors ensure precise temperature control during manufacturing. For example:
- Industrial models protect materials in processes like plastic moulding or food production.
- Monitoring systems help maintain environmental stability in complex setups.
Logistics
In temperature-sensitive environments, temperature monitors and alarms protect perishables in transit. Real-time alerts signal if temperatures rise, safeguarding valuable shipments.
Healthcare
Hospitals use temperature sensors to monitor vaccine storage, ensuring compliance with regulatory requirements. Maintaining the right humidity and temperature range in critical areas prevents damage to sensitive equipment.
Key Features to Look For
When choosing a remote temperature monitoring system, consider these features:
- Wireless Technology: Ensure the system uses reliable Wi-Fi or other wireless technologies for data transmission.
- Battery Life: Long-lasting battery life ensures uninterrupted monitoring in remote locations.
- Ease of Use: Systems should be plug-and-play, requiring minimal setup.
- Integration: Compatibility with existing monitoring software improves efficiency.
- Range: A good system should cover the entire operational area, from small units to large-scale industrial models.
The Future of Remote Temperature Monitoring
Emerging technology is shaping the future of remote monitoring:
- AI-Driven Systems: Enhanced monitoring software uses AI for predictive analytics, identifying trends and preventing failures.
- Edge Computing: Enables faster analysis and response by processing data locally.
- Advanced Devices: Modern wireless temperature sensors now include additional capabilities like monitoring humidity and extending battery life.
As innovations like smart sensors and IoT-enabled devices advance, remote temperature monitoring systems will become more efficient and reliable across various applications.
Conclusion
Remote temperature monitoring systems are essential for maintaining safety, optimising operational efficiency, and ensuring regulatory compliance. By using wireless temperature sensors and advanced monitoring software, industries can protect their equipment, improve conditions in temperature-sensitive environments, and save energy. For expert solutions tailored to your needs, consult Controls Traders today.
Frequently Asked Questions
What is remote temperature monitoring used for in industrial settings?
Remote monitoring systems maintain safe temperature ranges, protecting equipment and ensuring compliance in temperature-sensitive environments.
How does a wireless remote temperature monitoring system work?
It uses sensors to collect temperature data and transmits it via Wi-Fi or cellular networks to monitoring software, which issues real-time alerts.
What are the benefits of integrating remote temperature monitoring systems with IoT?
IoT integration enhances temperature monitoring through advanced analytics, predictive maintenance, and better control of industrial models.
How do I choose the right remote temperature monitoring system for my facility?
Look for features like sensor accuracy, battery life, compatibility with existing systems, and wireless technology.
Are remote temperature monitoring systems cost-effective?
Yes, they help save energy, minimise downtime, and extend the life of equipment, making them a valuable investment.
Read more
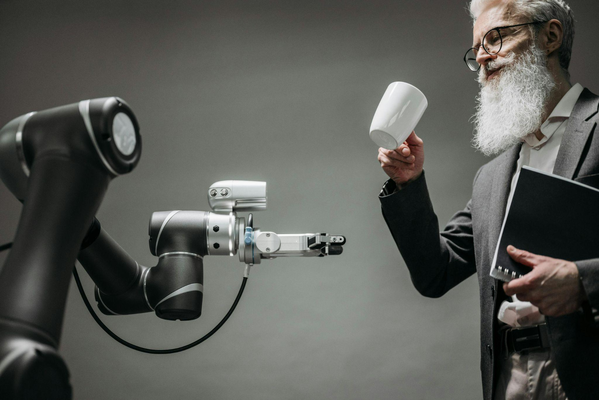
HMI or Human Machine Interface: A Comprehensive Guide
Human Machine Interface (HMI) has become a cornerstone of modern industrial control systems. By serving as the communication bridge between operators and machinery, HMIs enhance productivity, safety, and operational efficiency. According to Controls Traders, known for its innovative solutions in industrial technologies, HMI panels play a vital role in fostering safe, reliable, and effective work environments.
What is HMI? Definition and Core Applications
So, what does HMI mean? Human-machine interface (HMI) is the technology that facilitates interaction between humans and machines, providing a user-friendly platform for monitoring and controlling industrial processes. According to industry experts, HMI screens empower operators to manage operations effectively, from straightforward tasks to complex automation.
Core Applications:
- Manufacturing: HMI panels provide real-time data and control for production line management, ensuring operational efficiency and reduced downtime.
- Energy Sector: HMI displays are essential for grid management and energy distribution monitoring, supporting a stable and reliable energy flow.
- Logistics: Human Machine Interfaces automate warehouse operations and enhance inventory management through accurate tracking and visualisation.
Common HMI tools include touch panels, graphical user interfaces (GUIs), and integrated HMI displays that interface with PLCs (Programmable Logic Controllers) and other industrial control units.
The Evolution of HMI Technology
HMI technology has significantly evolved, shifting from basic mechanical controls to advanced touch-based and AI-integrated systems. According to Tech Trends Journal, early control systems in the 20th century relied on mechanical switches and indicator lights for basic operations. The introduction of text-based terminals in the 1980s began the shift towards more interactive systems, allowing limited operator interactions.
Key Milestones:
- 1980s: The introduction of text-based terminals began the era of limited interactive HMI screens.
- 1990s-2000s: The emergence of graphical touchscreens revolutionised the field, enabling more complex and visually driven interactions.
- Present Day: HMIs now incorporate AI and cloud technology, offering adaptive, remote-capable, and predictive interfaces that align with digital transformation trends.
Key Features and Benefits of Modern HMI Systems
Modern HMI systems featuring advanced HMI design, enhance operational control and efficiency.
Key Features:
- Real-time Data Visualisation: Operators can see and respond to data instantly, allowing for informed decision-making.
- Custom Interfaces: Flexible layouts tailored to specific processes and operational needs.
- User Accessibility: Intuitive HMI panel for easy navigation and quick onboarding.
- Adaptive Layouts: Configurable displays that evolve with process requirements.
Benefits:
- Enhanced Safety: Integrated safety alarms and alerts notify operators of system anomalies.
- Operational Efficiency: Simplifies complex processes and allows for rapid response to issues.
- Data Analytics Tools: Facilitates predictive maintenance by identifying performance patterns.
- Remote Monitoring: Ensures continuous oversight through remote access, supporting varied operational scenarios.
Applications of HMI in Different Industries
The adaptability of HMI systems allows for their use across various industries, enhancing process optimisation and reducing downtime.
Industry Examples:
- Manufacturing Plants: Real-time HMI displays help monitor production lines, enabling quick adjustments to prevent bottlenecks and delays.
- Energy Facilities: Operators use HMI screens to monitor and control energy outputs, maintaining consistent and reliable distribution.
- Logistics Centres: HMI panels with dashboards track inventory and coordinate vehicle movement, reducing errors and enhancing throughput.
According to a study published by Industry Solutions Weekly, companies using HMI dashboards have significantly improved operational transparency and reduced system failures.
Best Practices for HMI Design and Implementation
The effectiveness of HMI systems largely depends on user-focused HMI design and careful implementation.
Guidelines:
- User Experience (UX) Design Priority: Ensure intuitive and straightforward interfaces.
- Customisation Options: Adaptable configurations to meet specific operational needs.
- Training and Education: Comprehensive training programs maximise system potential.
- Software Compatibility: Seamless integration of HMI software with existing control systems.
- Feedback and Iteration: Regular user feedback to refine the interface.
Challenges and Future Prospects of HMI Technology
Despite many advantages, HMI technology faces challenges and holds promising prospects for the future.
Current Challenges:
- Cybersecurity Risks: Data security must be ensured as HMIs connect to larger networks.
- Legacy System Integration: Compatibility issues with older equipment.
- Complexity in Design: Balancing feature-rich interfaces with user-friendliness.
Future Trends:
- AI-Enhanced Interfaces: Machine learning will drive predictive functions and smarter decision-making.
- Augmented Reality (AR): AR could provide enhanced training and maintenance directly through HMI displays.
- Cloud Connectivity: Expanded cloud-based capabilities for real-time remote access.
The future of HMI points towards smarter, more connected systems that seamlessly integrate with cloud and augmented technologies, promoting productivity and connectivity.
Conclusion
HMI technology has become critical in modern industries, offering real-time control, increased safety, and greater process efficiency. Adopting advanced HMI solutions is essential for companies seeking operational excellence and competitive advantage. As industries progress towards higher levels of automation, embracing cutting-edge HMI technologies positions organisations to optimise their workflows, reduce downtime, and enhance overall productivity.
Explore how Controls Traders can support your HMI needs with expert solutions tailored for the industrial sector. Visit Controls Traders to discover premium HMI products and services that elevate your operations with reliability and innovation. Connect with our team to find the right HMI solution for your business.
FAQs
What does HMI stand for in industrial automation?
HMI stands for Human Machine Interface, facilitating communication between humans and machines.
How does an HMI differ from a PLC?
An HMI is an interactive user interface, while a PLC is an automated system for executing control functions.
What are the key benefits of using HMI in industrial processes?
Improved safety, real-time data access, and streamlined process management.
What challenges exist when implementing HMI technology?
Challenges include cybersecurity, legacy system integration, and design complexity.
What future trends can we expect in HMI technology?
AI-driven enhancements, augmented reality, and cloud-based solutions.
Read more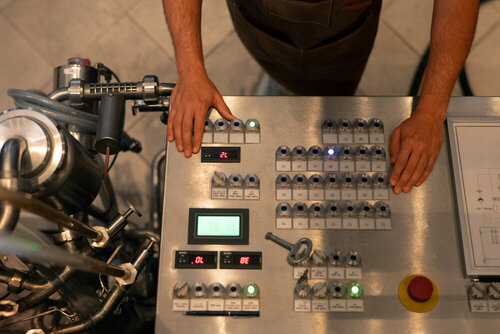
What Are The Different Types of Actuators and Their Applications
Actuators are essential in industrial control systems, converting energy into mechanical motion. Their role in automation and energy conversion helps industries optimise performance, ensuring smoother, more efficient operations. Understanding actuator types aids engineers, facility managers, and manufacturing professionals in selecting the best solutions.
Understanding Different Types of Actuators – A Fundamental Overview
An actuator is a device that converts energy (electric, hydraulic, pneumatic) into mechanical motion. This energy transformation enables movement in systems that control industrial processes and automation. Actuators are responsible for executing commands within control systems, powering everything from robotic arms to valve operations.
Actuators receive input energy and convert it into an output motion. Depending on the actuator type, this motion can be linear or rotary. For instance, electrical energy powers electric actuators, while fluid pressure drives hydraulic actuators. Understanding these principles helps grasp their role in modern industry.
Linear vs. Rotary Actuators
Differences Between Linear and Rotary Actuators
- Linear Actuators: Produce straight-line motion. Common in conveyor systems, robotic arms, and industrial packaging, they enable precise, repeatable movement.
- Rotary Actuators: Generate circular motion and are vital for rotating machinery parts, automated valves, and assembly lines.
Examples in Industrial Applications
- Linear Actuators: Used in positioning and lifting mechanisms, as seen in assembly robots.
- Rotary Actuators: Essential for rotation processes, such as turning arms in production machinery.
Pneumatic Actuators – Speed and Efficiency
Structure and Characteristics of Pneumatic Actuators
Pneumatic actuators operate using compressed air, enabling fast and repetitive movements. They are known for their simplicity, high-speed operation, and low cost. These actuators are often lightweight and adaptable for various industrial tasks.
Applications
Pneumatic actuators excel in applications requiring rapid, cyclic operations, such as in packaging and bottling plants. Their efficiency makes them suitable for tasks where consistent movement is essential.
Hydraulic Actuators – Power and Precision
The Power of Hydraulic Actuators
Hydraulic actuators leverage fluid pressure to create motion, offering significant force output that is ideal for heavy-duty applications. Their precision and strength are unmatched, making them indispensable for heavy machinery tasks.
Industrial Use Cases
Hydraulic actuators are used in construction equipment like excavators and cranes, where substantial force and precision are needed to lift or move heavy loads. Their robust design ensures reliable operation under high-load conditions.
Electric Actuators – Precision and Control
Benefits of Electric Actuators
Electric actuators offer precise control and are generally low-maintenance. These actuators are powered by electric motors, which are ideal for tasks requiring exact movements and integration with digital control systems.
Practical Applications
Electric actuators are used in automated industrial processes where precision is a priority, such as robotics and conveyor systems. They also support smart systems through programmable controls, enhancing operational flexibility.
Comparing Actuator Types – Selection Guide
Actuator Comparison Table
|
|
|
|
|
|
|
|
|
|
|
|
|
|
|
|
|
|
|
|
Choosing the Right Actuator
Select an actuator by evaluating operational speed, force requirements, and environment. Pneumatic actuators suit high-speed, low-force tasks, while hydraulic ones are best for powerful, precise operations. Electric actuators are ideal for applications needing exact control.
Key Considerations When Choosing an Actuator
Critical Factors for Selection
- Load Capacity: Assess the force an actuator needs to handle.
- Operational Speed: Choose pneumatic for rapid cycles, hydraulic for power, and electric for controlled motion.
- Environment: Consider exposure to temperature extremes, moisture, or dust.
- Maintenance Expectations: Hydraulic actuators require more upkeep than electric or pneumatic options.
Real-World Applications of Different Actuators
Industrial Use Cases
- Pneumatic Actuators: Utilized in packaging machines where speed and repeatability are key.
- Hydraulic Actuators: Found in construction vehicles and presses due to their power capacity.
- Electric Actuators: Applied in robotic arms for precision assembly and automated adjustments.
Specific Industry Examples
- Manufacturing: Linear actuators in robotic welding.
- Construction: Hydraulic systems in cranes.
- Electronics: Electric actuators in automated testing machines.
Future Trends in Actuator Technology
Advancements Shaping the Industry
Integrating smart actuators and IoT is driving the future of industrial automation. These modern actuators offer enhanced data collection, enabling predictive maintenance and energy savings. The push for eco-friendly and energy-efficient actuators influences the shift towards electric models.
Energy Efficiency and Sustainability
Future trends indicate a move toward sustainable actuators that consume less energy and incorporate recyclable materials. Industries are increasingly adopting electric actuators because they are compatible with renewable energy sources and smart grids.
Conclusion
Actuators are pivotal for industrial processes due to their diverse types and capabilities. Understanding the benefits and limitations of pneumatic, hydraulic, and electric actuators helps select the most suitable solution for optimising operations.
Explore Controls Traders’ extensive range of actuators or contact their expert team for tailored advice in choosing the right actuator for your needs.
FAQs
What is the best type of actuator for high-speed operations?
Pneumatic actuators are ideal due to their rapid movement and cost-effectiveness.
How do hydraulic actuators compare to electric actuators in terms of maintenance?
Hydraulic actuators require more maintenance due to fluid handling and potential leaks, whereas electric actuators are low maintenance and reliable.
Are electric actuators cost-effective for long-term use?
Yes, despite higher initial costs, electric actuators offer long-term savings in energy and maintenance.
Can I use actuators in harsh outdoor environments?
Hydraulic actuators perform well in rugged conditions, while pneumatic actuators are robust but require dry air to avoid corrosion.
What are the most common applications for linear actuators?
Due to their precise linear motion, linear actuators, such as conveyor lines and robotic arms, are essential in automation systems.
Read more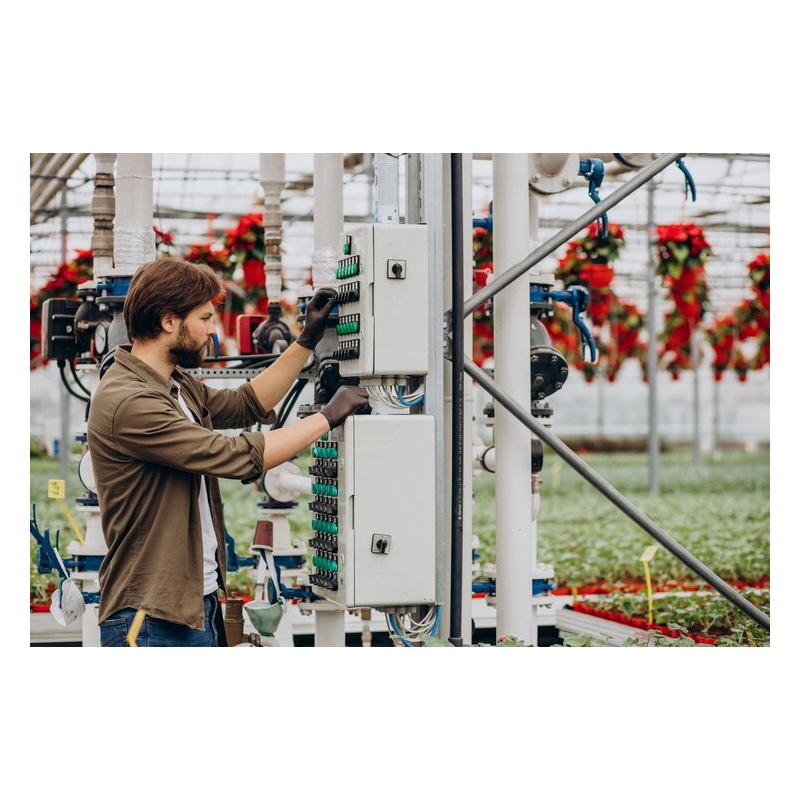
Voltage Converters: Learn How They Work and How to Pick the Best Type
Voltage converters serve as pivotal devices in the field of electrical engineering, enabling the transformation of electrical output to suit various voltage requirements. Their role spans from powering essential household appliances to stabilising industrial equipment. Choosing the right converter hinges not only on understanding the mechanics of step-up and step-down conversions but also on evaluating efficiency, size, and built-in safety features. This exploration into voltage converters will provide insights into their operation and guide on selecting the most suitable type for your specific applications, ensuring both performance and safety are uncompromised.
What is a voltage converter?
According to Controls Traders a voltage converter is a device that changes the electrical output of a power source to a different voltage level.
Voltage converters come in various forms, such as step-up converters, which increase the input voltage, and step-down transformers, which decrease it. These devices are essential in adapting power supplies to the requirements of different electrical systems and appliances.
Common uses include power adapters for electronic devices, voltage stabilisers for consistent power delivery, and travel adapters for compatibility with international voltage standards.
Voltage regulators within these converters guarantee stable output voltage, preventing damage to sensitive equipment.
Whether for industrial applications or personal electronics, voltage converters play a critical role in guaranteeing safe and efficient power management.
How does a voltage converter work?
Voltage converters function by utilising electronic circuits to alter the input voltage to the desired output level. At the core of a voltage converter, electronic components facilitate voltage transformation.
In transformers, the primary coil receives the mains voltage, and through electromagnetic induction, the secondary coil delivers the altered voltage. A step up transformer increases the voltage, while a step down transformer decreases it.
For more precise control, switching voltage regulators are employed. These power converters rapidly switch on and off, controlling the duty cycle to achieve the desired output.
What types of voltage converters are there?
Several types of voltage converters are available, each designed to meet specific requirements and applications.
A voltage transformer adjusts the voltage level in AC circuits.
Power inverters, including sine wave inverters and modified sine wave inverters, convert DC to AC power.
Stepdown voltage converters reduce higher voltage to a lower level.
DC to DC converters are used for voltage adjustments within DC circuits.
Travel adapter converters facilitate the use of electrical devices across different countries.
Voltage stabilisers maintain a consistent voltage level, protecting sensitive equipment.
Frequency converters adjust the frequency of the electrical current.
Voltage regulators guarantee stable output voltage despite fluctuations in input.
Each type serves distinct purposes, making it essential to select the appropriate converter for your needs.
What's the difference between step-up and step-down converters?
Understanding the difference between step-up and step-down converters is key to selecting the appropriate device for voltage adjustment needs.
A step-up converter increases the input voltage range to higher output voltages, while a step-down converter decreases it, acting as a voltage reducer. These devices are essential for various applications requiring different transformers voltage.
A step-up converter is useful when the destination device needs a higher voltage than what is available. Conversely, a step-down converter fits scenarios where the needed output voltage is lower than the input.
Power voltage converters, including dual voltage models, guarantee compatibility between devices with differing voltage requirements, preventing damage and guaranteeing efficient operation.
Selecting the correct type depends on specific voltage conversion needs.
How do I choose the right voltage converter?
Choosing the right voltage converter involves understanding its common applications, evaluating essential features, and examining its capability to handle different power outputs.
Identifying the specific requirements of your devices will guide you in selecting an appropriate converter.
Additionally, considering factors such as efficiency, size, and safety features will guarantee peak performance and reliability.
What are common uses for voltage converters?
Voltage converters are vital for adapting electrical devices to different power standards, making them indispensable for international travel, industrial machinery, and consumer electronics.
Travellers often rely on travel adapters to guarantee their electronic devices function correctly overseas.
A DC-DC converter enables efficient power management in low-voltage applications, providing stable voltage output.
Industrial machinery frequently uses step-down voltage converters to match equipment power requirements.
Plug adapters simplify compatibility between differing power voltage standards.
In addition, voltage converters with built-in short-circuit protection enhance safety and reliability.
What are the features of a good voltage converter?
A quality voltage converter should offer key features such as efficiency, reliability, and compatibility with the intended application. The converter must handle various voltage levels and power supplies effectively.
An efficient transformer guarantees minimal energy loss, while a clean sine wave output is vital for sensitive electronics. Built-in safety protections prevent damage to connected devices. Voltage regulators maintain stable output despite fluctuations.
The converter should be compatible with various power plugs and come with travel plug adapters for international use. Confirming that the converter supports all your compatible devices is fundamental.
These features collectively determine the performance and safety of a voltage converter, making it suitable for diverse applications.
How does a voltage converter handle different power outputs?
To handle different power outputs effectively, a voltage converter must be designed with the specific voltage and current requirements of the devices it will power.
The power supply must accommodate varying voltage levels and guarantee proper voltage regulation.
Switch mode power converters are often preferred for their efficiency in managing electrical current.
When selecting a voltage converter, consider the device's power outputs, especially for voltage-sensitive equipment and power tools.
The converter must match the voltage and current ratings to prevent damage.
Choose a converter that offers reliable voltage regulation to maintain steady performance under different loads.
Proper selection guarantees the longevity and proper functioning of your power tools and other voltage-sensitive devices.
What safety measures are needed for voltage converters?
Proper installation, recognising signs of malfunction, and effective troubleshooting are essential safety measures when using voltage converters.
Ensuring the converter is installed correctly minimises electrical risks.
Additionally, being able to identify and address issues promptly can prevent potential hazards.
How do I install a voltage converter?
Installing a voltage converter requires careful attention to safety protocols to prevent electrical hazards and guarantee proper operation.
Begin by consulting the user guide to understand the voltage converter's specifications. Ascertain the input voltage matches your power supply and verify the output voltage corresponds to your device's requirements. If a plug adapter is needed, secure it firmly before connecting.
When dealing with step-down voltage converters, confirm the voltage levels are appropriate for your equipment. Implement all safety precautions, such as unplugging the power supply before making connections and avoiding contact with metal parts.
Adhere strictly to the manufacturer's guidelines throughout the installation process to ascertain safe and effective operation of your voltage converter.
What are the signs of a faulty voltage converter?
Identifying a faulty voltage converter is essential for maintaining safety and ensuring the proper functioning of your electrical devices.
Common signs of malfunction include irregular voltage levels, which can lead to power supply issues for connected devices. Overheating is another critical indicator, often resulting from internal component failure. Unusual noises, such as buzzing or humming, can also signal a problem. Voltage fluctuation is another sign to watch for, as it can harm sensitive equipment.
To mitigate risks, implement safety precautions like regular inspections and using devices within recommended voltage ranges. Ensuring that your voltage converter operates correctly will protect your electrical devices and enhance overall safety.
How do I troubleshoot voltage converter issues?
Addressing the signs of a faulty voltage converter requires systematic troubleshooting to pinpoint and resolve issues effectively.
Begin by checking the power supply to guarantee it provides continuous power without interruptions.
Inspect the voltage converter for any visible damage or signs of overheating.
Verify voltage regulation by measuring the output voltage; it should match the expected levels.
If experiencing over voltage or voltage issues, replace the fuse using a suitable fuse kit.
Confirm device compatibility, as mismatched devices can cause malfunction.
Test the power converter with another device to determine if the issue is with the converter or the connected device.
How long does a voltage converter last?
The lifespan of a voltage converter can vary based on usage, quality, and maintenance.
Proper upkeep is essential to guarantee long-term functionality.
Regular cleaning, avoiding overloading, and adhering to the manufacturer's guidelines are critical practices.
How do I maintain a voltage converter for long-term use?
To guarantee long-term use of a voltage converter, regular maintenance and understanding its impact on device compatibility and energy efficiency are essential.
Proper upkeep involves periodic checks and adherence to manufacturer guidelines.
Additionally, a well-maintained voltage converter can greatly enhance device performance and reduce energy consumption, contributing to its longevity.
How does a voltage converter affect device compatibility?
Frequently, a voltage converter plays an essential role in ensuring that electrical devices from different regions operate safely and efficiently.
By adjusting voltage levels through a power converter, it matches power supplies to device requirements.
Whether using a voltage doubler or adapting travel voltage, ensuring device compatibility involves considering outlet power, charging ports, and the correct adapter plug, safeguarding your electronics.
How does a voltage converter impact energy efficiency?
Understanding energy efficiency in voltage converters involves examining their design, operation, and maintenance.
Efficient voltage regulators and power converters guarantee minimal energy loss in power supplies.
Voltage dividers and direct power supplies must handle watt voltage effectively for peak performance.
High-quality voltage converters improve the energy efficiency of power tools, reducing wastage and enhancing overall system reliability.
Read more
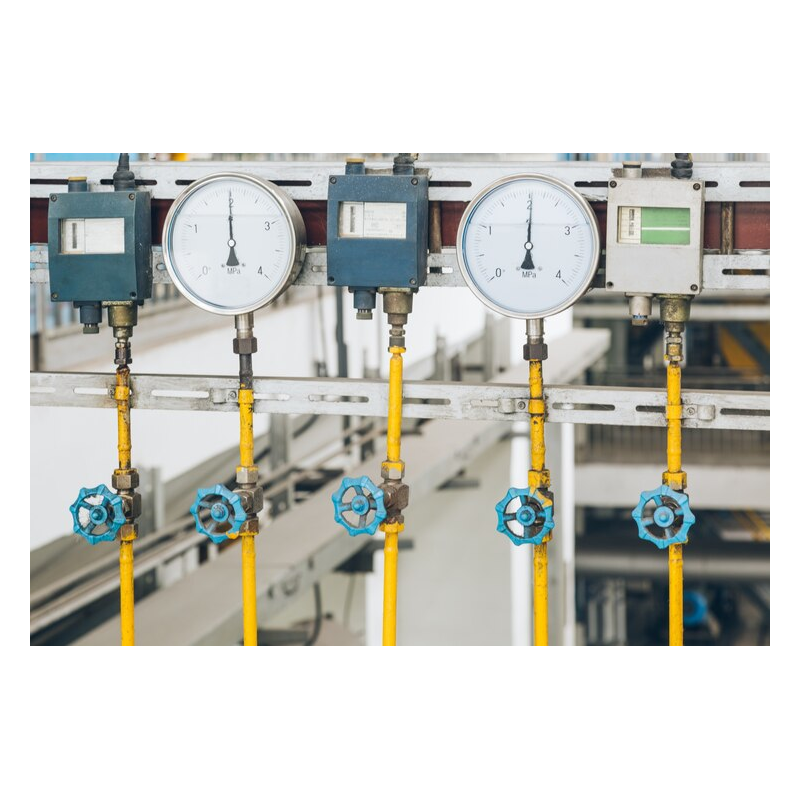
Pressure Switch: Functionality, Types, Applications, Calibration and Safety Features
Understanding the multifaceted role of pressure switches is critical for industries reliant on precise pressure management. These devices, integral to systems ranging from water pumps to air compressors, operate by activating or deactivating circuits in response to pressure changes. The diversity of pressure switches—mechanical, electronic, and differential—ensures suitability across varied applications. Accurate calibration, achieved through specialised tools, is paramount for maintaining operational reliability. Additionally, safety features like interlocks and pressure cutout mechanisms are imperative to prevent failures. To comprehend their full impact and functionality, one must explore their types, applications, and safety protocols in greater detail.
What is a Pressure Switch?
According to Controls Traders, a pressure switch is an electrical device designed to monitor and respond to changes in pressure within a system. It operates by detecting when the pressure reaches a predefined threshold and then activating or deactivating a circuit.
There are two main types: mechanical pressure switches and electronic pressure switches. Mechanical switches use physical mechanisms, while electronic switches utilise pressure sensors.
These devices can monitor various pressure types, such as air pressure and differential pressure. Pressure setting ranges determine the specific pressures at which the switch operates.
Proper pressure calibration guarantees accuracy and reliability. Safety features are integral, preventing system failures and guaranteeing operational efficiency.
Pressure switches are essential in maintaining system integrity and performance in numerous applications.
How Does a Pressure Switch Work?
Understanding the inner workings of a pressure switch involves examining its key components and the mechanisms they utilise to detect and respond to pressure changes. A pressure switch typically consists of a sensor that measures pressure, an electromechanical mechanism to convert pressure changes into electrical signals, and an adjustment range to set specific pressure thresholds.
When the sensed pressure reaches a pre-set level, the switch activates or deactivates an electrical circuit. Calibration guarantees accurate functionality and is essential for maintaining safety features across various applications.
Differential pressure switches operate on similar principles but measure the difference between two pressure points. Their reliability and precision make them indispensable in many industrial and commercial settings.
What are the Types of Pressure Switches?
Several distinct types of pressure switches cater to various industrial and commercial needs.
Mechanical pressure switches operate using a diaphragm or piston mechanism to detect pressure changes.
Electronic pressure switches utilise sensors and digital interfaces for more precise control and monitoring.
Differential pressure switches measure the difference between two pressure points, ensuring accurate readings across a specified pressure range.
Each type has unique calibration requirements and safety features tailored to their specific applications.
Mechanical switches are often preferred for their simplicity, while electronic options offer advanced switching functions and higher precision.
Understanding these types is essential for selecting the right pressure switch for your system's needs and ensuring peak performance and safety.
What Materials are Used in Pressure Switches?
Pressure switches are constructed from various materials to guarantee durability, reliability, and compatibility with different environments and media.
Stainless steel and brass are commonly used for components in contact with media, known as the wetted area, due to their corrosion resistance and strength.
Diaphragms within pressure switches often utilise flexible materials like rubber or metal to detect changes in hydraulic pressure or air pressure switches.
Sensors and pressure transducers are typically made from robust materials to withstand harsh environments.
Electrical contacts, essential for signal transmission, are often crafted from conductive metals.
The choice of materials guarantees the pressure switch performs reliably under varying conditions and extends its operational lifespan.
What are the Physical Dimensions of a Pressure Switch?
When considering the physical dimensions of a pressure switch, it is vital to recognise that these devices can vary considerably in size depending on their specific application and design requirements.
Pressure switches can range from compact designs for limited space applications to larger models suitable for high-pressure capacities.
The physical dimensions are influenced by the type of pressure sensor, safety features, and the inclusion of an adjustment screw for calibration.
Different types of pressure switches cater to various applications, each with unique space constraints and functional demands.
Understanding the physical dimensions is essential for proper installation and ensuring that the pressure switch meets the specific needs of the system it is integrated with.
How to Install a Pressure Switch?
Installing a pressure switch involves gathering the necessary tools and following a series of methodical steps.
Essential tools typically include wrenches, screwdrivers, and a pressure gauge.
The installation process encompasses mounting the switch, connecting wiring, and calibrating the device to guarantee proper functionality.
What Tools are Needed to Install a Pressure Switch?
To install a pressure switch, a specific set of tools is required to guarantee proper functionality and safety.
Essential installation tools include a pressure gauge to monitor system pressure, a control valve for flow regulation, and a pressure regulator to maintain desired pressure levels.
Additionally, tools for connecting to the electrical circuit are necessary, such as wire strippers and screwdrivers.
For systems involving water pressure, float switches may be required. An air compressor can aid in pressurising the system for testing purposes.
Adhering to safety features is vital; hence, personal protective equipment (PPE) like gloves and safety glasses should be used.
Proper tools assure the pressure switch operates effectively and maintains system integrity.
What are the Steps to Install a Pressure Switch?
Proper installation of a pressure switch involves several systematic steps to guarantee reliable operation and system safety.
Start by ensuring the system is de-energised to meet safety features.
Identify the correct location for the pressure switch installation near the inlet pressure source.
Connect the pressure switch to the pneumatic or fluid pressure line, ensuring all fittings are secure.
Adjust the pressure settings according to system requirements.
Use a calibration device to verify accuracy.
Connect the electromechanical control pressure switch to the electrical system, following wiring diagrams.
Power up the system and test the pressure switch to confirm it responds correctly to changes in pressure.
What are Common Applications of Pressure Switches?
Pressure switches are commonly used in a variety of industrial, commercial, and residential applications to monitor and control pressure levels.
In water pumps, they guarantee proper pressure and prevent damage due to overpressure. Air suspension systems in vehicles utilise pressure switches to maintain ideal ride quality. Compressors use them to regulate air pressure and avoid system failures. In flow control, they help manage fluid dynamics in pipelines. Wastewater treatment facilities use pressure switches to maintain safe and efficient operations.
These devices are integral to automation control products, providing essential feedback and enabling automated responses. Safety features and precise calibration are critical in all these applications to guarantee reliability and performance.
How to Calibrate a Pressure Switch?
Calibrating a pressure switch requires specific equipment such as a pressure source, a calibrated pressure gauge, and adjustment tools.
The process involves setting the switch to the desired pressure range and fine-tuning the set points to guarantee accurate operation.
Following a systematic approach, involving precise steps, assures the switch functions reliably within its designated parameters.
What Equipment is Needed to Calibrate a Pressure Switch?
To calibrate a pressure switch, specific equipment such as a pressure source, a reference gauge, and a calibration device is essential. The pressure source provides the necessary psi for testing.
Pressure gauges and sensors guarantee precise pressure management by displaying accurate measurement values. Transducers convert pressure into an electrical signal that can be read by the calibration device.
This device compares the pressure switch's response to the known reference values, affirming its accuracy. Adjustable pressure settings on the calibration device allow for fine-tuning to match the desired operational parameters.
Proper calibration guarantees reliable performance, contributing to the overall safety and efficiency of any system using pressure switches.
What are the Steps to Calibrate a Pressure Switch?
Effective calibration of a pressure switch involves several methodical steps to ascertain accurate and reliable operation.
Begin by isolating the pressure switch from the system to guarantee safety. Connect a calibrated pressure source to the switch. Gradually apply mechanical pressure or electronic pressure until the switch point is reached.
Adjust the switch to the desired preset pressure level. Next, reduce the pressure to determine the reset point. Measure and record hysteresis, the difference between the switch point and reset point.
Make necessary adjustments to achieve peak performance. Repeat the process to confirm accuracy. Proper calibration enhances service life and guarantees reliable water pressure control.
Always follow manufacturer guidelines and use precise instruments for best results.
What are the Safety Features of a Pressure Switch?
A pressure switch incorporates several safety features designed to prevent system failures and guarantee reliable operation.
High pressure and low pressure switches are equipped with interlocks to protect equipment by shutting down systems when pressure levels exceed safe limits.
Pressure cutout mechanisms are essential for preventing over-pressurisation, which could lead to hazardous conditions.
In explosion-hazard environments, pressure switches are designed to minimise the risk of triggering explosions.
Additionally, maintaining consistent water pressure and managing pressure differentials are critical safety features that maintain system stability.
These features collectively enhance the reliability and safety of pressure switches across various applications, making them indispensable for maintaining operational integrity and preventing potential damage or accidents.
How to Troubleshoot a Pressure Switch?
When troubleshooting a pressure switch, it is essential to first identify common issues such as incorrect pressure settings, electrical faults, or mechanical wear.
Understanding the latest innovations in pressure switch technology, including digital interfaces and advanced diagnostics, can aid in more effective problem-solving.
Additionally, new materials like corrosion-resistant alloys and high-performance polymers enhance durability and reliability.
What are Common Issues with Pressure Switches?
Common issues with pressure switches often stem from improper calibration, electrical problems, or mechanical failures.
Calibration errors can lead to inaccurate pressure readings, affecting the performance of the pressure switch and associated systems.
Electrical problems, such as faulty wiring or loose connections, can disrupt the signal transmission between the pressure switch and control unit.
Mechanical failures, like worn-out diaphragms or clogged pressure ports, can prevent the pressure switch from operating correctly.
Pressure spikes and pump damage can occur if the sensor type electromechanical pressure switch fails to provide adequate protection on water pumps.
Regular maintenance and calibration are essential to guarantee the safety features and applications of pressure switches function effectively, mitigating common issues and maintaining system integrity.
What are the Latest Innovations in Pressure Switch Technology?
Advancements in pressure switch technology have led to the development of more accurate, reliable, and versatile devices suitable for a wide range of applications.
Among the latest innovations are digital displays and multicolour switching displays, enhancing functionality and user interface.
Modern electromechanical pressure switches now offer improved calibration features, guaranteeing precision and consistency.
These innovations enable more efficient monitoring and control in various types of applications, from industrial automation to HVAC systems.
Enhanced safety features have also been integrated, providing better protection against overpressure conditions.
These technological advancements guarantee that pressure switches remain indispensable tools for maintaining operational safety and efficiency.
What New Materials are Being Used in Pressure Switches?
Recent developments in material science have introduced advanced composites and high-performance alloys into the construction of pressure switches, greatly enhancing their durability and functionality.
These new materials improve the performance of components and sensors under extreme temperature conditions, making them ideal for specialist industry applications. Enhanced materials also contribute to more accurate calibration, resulting in better reliability and safety features.
In demanding environments, such as chemical processing or oil and gas extraction, these pressure switches exhibit resilience and precision, ensuring peak performance.
The integration of these advanced materials into pressure switch design reflects a significant step forward in meeting the rigorous demands of modern applications, ultimately broadening their scope of use and effectiveness.
Read more
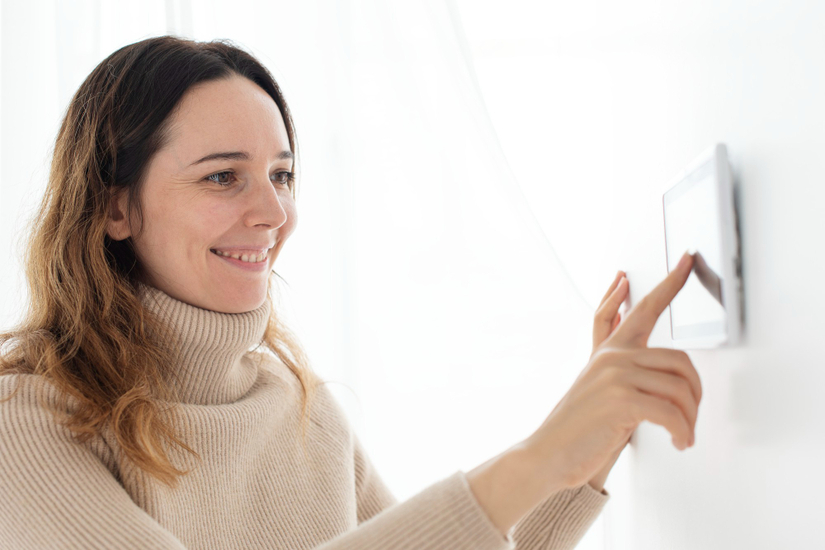
Comprehensive Guide to Stand-alone Controllers & Thermostats
Stand-alone controllers and thermostats are essential components in modern building automation systems. These smart HVAC controllers control various aspects of a building, such as temperature, humidity, and lighting.
This comprehensive guide will discuss everything you need to know about a stand-alone controller and thermostats and why they improve energy efficiency.
What Are Stand-alone Controllers?
Stand-alone controllers are designed to manage HVAC systems without installing a Building Management System (BMS). They control temperature, humidity, and air quality by directly interfacing with heating and cooling units. These standalone controllers are particularly beneficial in smaller buildings or remote locations where centralised control is impractical. However, larger systems tend to have issues with scalability to offer a balanced view.
What are the Key Features of Stand-alone Controllers?
Some of the critical features of a stand-alone access control system include:
- User-friendly interface: Stand-alone controllers typically have a simple and intuitive user interface, making them easy to operate.
- Programmability: These controllers can be programmed to follow specific schedules or adjust settings based on occupancy patterns, resulting in energy savings.
- Remote access: Some stand-alone controllers have remote access capabilities, allowing users to control the system from anywhere through a web or mobile application.
- Compatibility: Stand-alone controllers are compatible with various HVAC systems, making them suitable for multiple building types and sizes.
- Security features: These controllers have built-in features such as user authorisation, access control lists, and encryption to ensure the system's safety.
Types of Stand-alone Controllers
There are various types of stand-alone controllers.
- Temperature Control Valves (TCV): TCVs regulate water flow based on temperature settings. They ensure the HVAC system maintains the desired thermal performance even under varying load conditions. This type of control is crucial in applications where precise temperature management is essential.
- Pressure-Independent Control Valves (PICV): PICVs automatically adjust the water flow to maintain consistent performance despite changes in system pressure. They enhance energy efficiency by optimising flow rates according to real-time demands.
- Automatic Balancing Valves (ABV): ABVs help maintain proper flow rates by automatically adjusting to pressure fluctuations within the system. This ensures that each part of the HVAC system receives the appropriate amount of heating or cooling.
HVAC Thermostats: The Heart of Temperature Control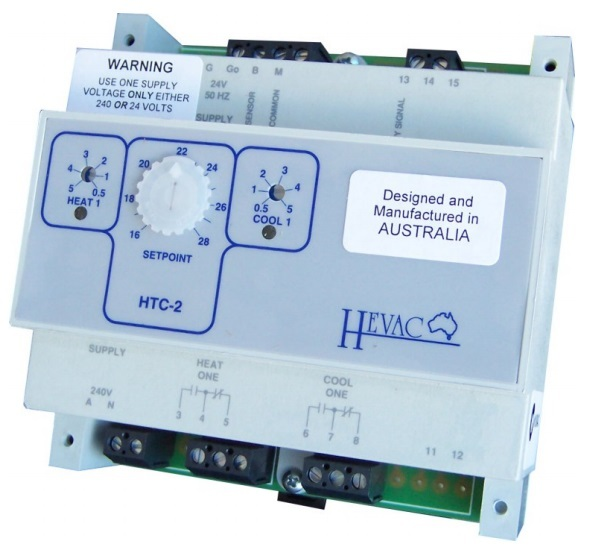
Thermostats are integral components within HVAC systems that monitor and regulate temperature. Stand-alone thermostats function independently, allowing users to set up desired temperatures without interfacing with a central control system. Smart thermostats have gained popularity recently due to their advanced features and benefits.
One of the main advantages of smart thermostats over traditional ones is their energy efficiency. They can automatically adjust the temperature based on usage and occupancy patterns, making them more efficient and convenient.
Types of HVAC Thermostats:
- On/Off Thermostats: These basic thermostats turn heating or cooling systems on or off based on a set temperature threshold. While straightforward, they can lead to temperature fluctuations. Examples include the Honeywell Pro Non-Programmable Digital Thermostat, a reliable choice for those seeking basic functionality with a backlit display for easy visibility. Users appreciate its simplicity and accuracy.
- Proportional Thermostats: Proportional thermostats provide more precise control by modulating system output based on current temperature readings. This results in improved comfort and energy efficiency. Popular brands include Ecobee Smart Thermostat Premium and Google Nest Learning Thermostat.
- Multi-Zone Thermostats: Designed for larger spaces, multi-zone thermostats allow for independent temperature control in different building areas. This zoning capability enhances comfort and reduces energy consumption. A well-known brand is the Honeywell Home T9 WiFi Smart Thermostat, which includes room sensors that detect occupancy and temperature.
Advantages of Stand-alone Controllers and Thermostats
- Flexibility: Stand-alone boost controller devices can be installed in various locations without extensive wiring or integration with existing systems.
- User-Friendly: Most stand-alone controllers feature intuitive interfaces that make it easy for users to adjust settings as needed.
- Reliability: With fewer components than centralised systems, stand-alone controllers often have lower failure rates.
Applications of Stand-alone Controllers and Thermostats
Stand-alone controllers and thermostats are widely used across the world in different sectors:
- Residential Buildings: Homeowners utilise stand-alone thermostats for efficient heating and cooling management.
- Commercial Spaces: Offices and retail environments benefit from multi-zone thermostats that cater to varying occupancy levels.
- Industrial Settings: In warehouses or manufacturing facilities, stand-alone units help maintain optimal product and personnel conditions.
- Remote Locations: Buildings without access to centralised control systems rely on stand-alone solutions for effective climate management.
How Can You Choose the Right Controller or Thermostat
When selecting a stand-alone thermostat for your HVAC system, consider the following factors:
- Application Needs: Assess whether you require basic on/off control or more advanced proportional control features.
- System Compatibility: Ensure the chosen device is compatible with your HVAC equipment.
- User Interface: Look for intuitive controls that match your comfort level with technology.
- Energy Efficiency Features: Consider devices that offer energy-saving modes or innovative capabilities for enhanced efficiency.
Comparison Table: Cost vs. Features of Controllers/Thermostats
|
|
|
|
|
|
|
|
|
|
|
|
|
|
|
|
|
|
|
|
|
|
|
|
|
|
|
|
|
|
|
|
|
|
|
|
Wrap Up
Stand-alone controllers and HVAC thermostats are essential for managing indoor climates effectively and efficiently. Their independence from centralised systems allows for greater flexibility in operation, cost savings, and user convenience. By understanding the various types available and their specific applications, users can make informed decisions that enhance comfort while optimising energy use in their buildings.
FAQs
Can stand-alone controllers work with any HVAC system?
Most stand-alone controllers are compatible with various HVAC systems, but it's always best to check for compatibility before purchasing.
How do stand-alone thermostats differ from centralised control systems?
Stand-alone thermostats operate independently and can be installed in various locations without extensive wiring or integration with existing systems. In contrast, centralised control systems require more complex installation and management processes.
Are there any maintenance requirements for stand-alone controllers and thermostats?
Like any other HVAC equipment, stand-alone controllers and thermostats require regular maintenance to ensure optimal performance and longevity. The manufacturer's guidelines provide specific maintenance recommendations.
Can stand-alone controllers and thermostats be integrated into a centralised control system?
Stand-alone controllers and thermostats can sometimes be integrated into a centralised control system for more comprehensive management. However, this may require additional equipment and professional installation.
Do stand-alone controllers and thermostats have any energy-saving features?
Many stand-alone controllers and thermostats offer energy-saving modes or advanced features to optimise energy use within the HVAC system. Be sure to research different options to find the most suitable one for your needs.
Can stand-alone controllers integrate with smart home systems like Google Home or Amazon Alexa?
Yes, many modern stand-alone controllers are designed to be compatible with smart home ecosystems, enhancing user convenience and control options.
Read more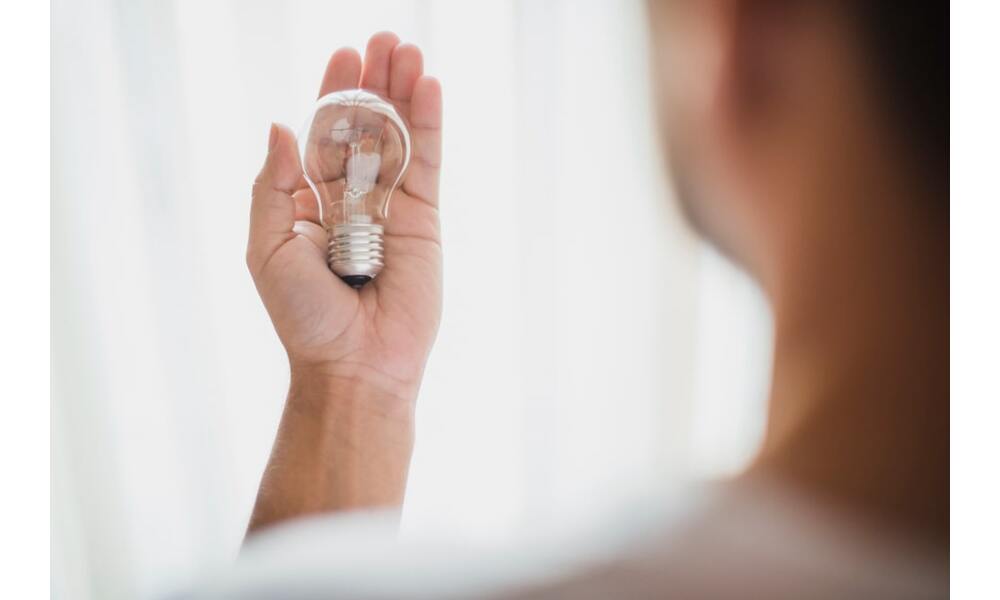
Smart HVAC Controllers for Commercial Use: Top Solutions for Energy Efficiency
Smart HVAC controllers for commercial use are increasingly vital in commercial settings. They provide enhanced energy efficiency, cost savings, and improved comfort. These systems leverage advanced technology to optimise heating, ventilation, and air conditioning, addressing the significant energy consumption typical of commercial buildings.
What are the Benefits of Smart HVAC Controllers?
Smart HVAC controllers offer a range of advantages that enhance energy efficiency, comfort, and overall system performance in commercial buildings. Here are the key benefits:
- Enhanced Energy Efficiency: Commercial HVAC control systems optimise energy use through real-time adjustments based on occupancy and environmental conditions, achieving energy savings of up to 20% or more than traditional systems.
- Improved Comfort and Productivity: These systems maintain precise temperature control, adapting to user preferences and ensuring a comfortable environment that can boost workplace productivity.
- Extended Lifespan of HVAC Systems: Predictive maintenance features monitor system performance and alert users to potential issues, helping to prolong equipment lifespan and reduce repair costs.
- Increased Security with Remote Monitoring: Remote access allows building managers to monitor HVAC operations in real time, enhancing security with alerts for unusual activities.
- Cost Reduction through Optimized Energy Consumption: Intelligent HVAC systems significantly lower utility bills by adjusting operations around peak energy usage times, providing financial benefits over time.
Smart HVAC controllers are integral to modernising heating and cooling systems in commercial buildings. They enhance energy efficiency and comfort and extend the lifespan of equipment while providing cost savings and improved security through advanced monitoring capabilities.
Types of Smart HVAC Controllers
Smart HVAC controllers come in various types, each offering unique features to enhance energy efficiency and user convenience:
- Wi-Fi-enabled thermostats allow remote access and control via smartphones or tablets, enabling users to adjust settings from anywhere.
- Smart Thermostats with Built-in Sensors: Equipped with sensors for monitoring temperature and humidity, these thermostats can optimise indoor climate based on real-time conditions
- Integrated Building Management Systems (BMS): These systems provide comprehensive control over HVAC, lighting, and other building systems, facilitating centralised management for extensive facilities.
- Cloud-based HVAC Controllers: These controllers utilise cloud technology to enhance performance tracking and energy management by offering real-time monitoring and analytics.
- Voice-controlled thermostats: These thermostats are compatible with Google Assistant and Amazon Alexa, enabling hands-free operation through voice commands, making home automation convenient.
Key Features of Smart HVAC Controllers
Here are the key features of Smart HVAC controllers.
- Energy Efficiency Features: Smart HVAC controllers offer advanced scheduling and geofencing capabilities to optimise energy consumption based on user patterns and occupancy.
- Remote Control and Monitoring: Users can control HVAC systems remotely via mobile apps, allowing adjustments from anywhere and enhancing convenience and energy management.
- Advanced Sensors: Equipped with sensors for temperature, humidity, and air quality monitoring, these systems gather real-time data to ensure optimal indoor conditions.
- Integration with Smart Devices: Smart HVAC systems can seamlessly integrate with other smart home devices, enabling coordinated control for improved efficiency.
- Customisable Features: Users can customise commercial HVAC control settings to meet specific comfort needs, utilising features like learning algorithms that adapt to individual preferences over time.
Final Wrap
Smart HVAC controllers are a crucial component of energy-efficient commercial buildings. They offer a range of benefits, including energy efficiency, comfort, and security. Various smart HVAC controllers are available, each with unique features and benefits. Building management systems (BMS) offer comprehensive control and monitoring of HVAC systems. Implementing smart HVAC controllers requires careful planning and execution but offers long-term benefits and savings.
FAQ
How do Smart HVAC Controllers improve energy efficiency?
They utilise real-time data from sensors to adjust heating and cooling based on occupancy and environmental conditions, potentially saving up to 20% on energy costs compared to traditional systems.
What types of Smart HVAC Controllers are available?
Common types include Wi-Fi-enabled thermostats, smart thermostats with built-in sensors, integrated building management systems (BMS), cloud-based controllers, and voice-controlled thermostats
Can Smart HVAC Controllers be monitored remotely?
Yes, many innovative HVAC systems offer remote monitoring capabilities, allowing facility managers to control and adjust settings via mobile apps from anywhere
What are the key features of Smart HVAC Controllers?
Key features include advanced scheduling, geofencing, remote control, integration with other smart devices, and customisable settings that adapt to user preferences
Do Smart HVAC Controllers require unique installation?
While some systems can be easily installed by users, others may require professional installation for optimal integration with existing building systems
Read more
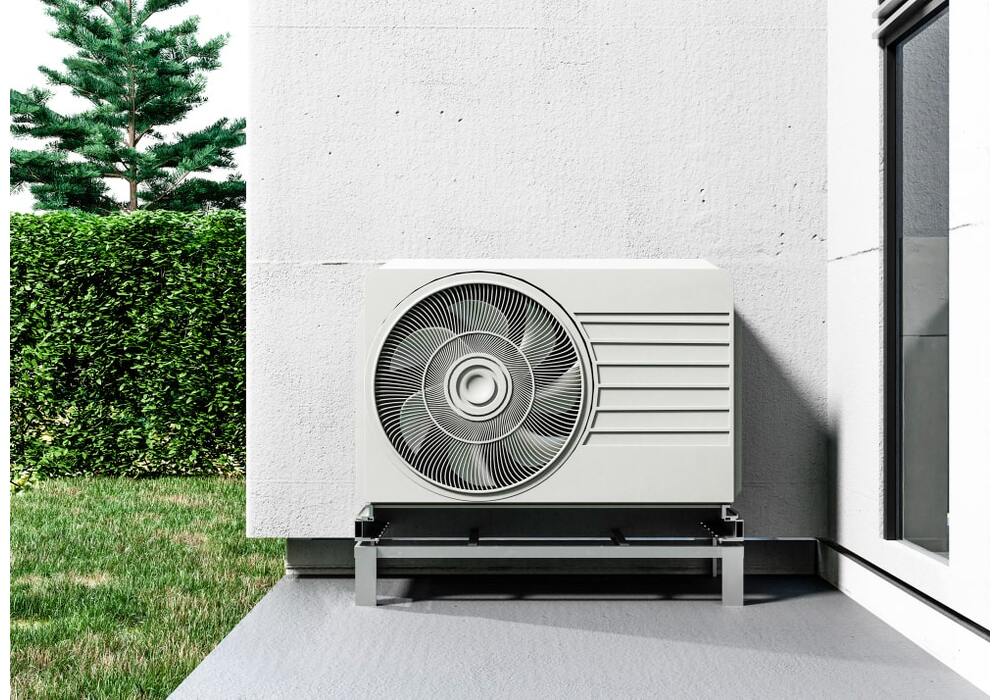
The Role of Smart HVAC Controllers in Energy Efficiency for Commercial Buildings
Nowadays, when energy efficiency is paramount, commercial buildings increasingly turn to technology to optimise their heating, ventilation, and even air conditioning unit (HVAC) systems to save money. The intelligent HVAC controller is one of the most significant advancements in this area.
This piece by Control Traders explores the role of intelligent HVAC controllers in home climate and enhancing energy efficiency, their benefits, types, features, installation, maintenance, and their integration into smart home systems.
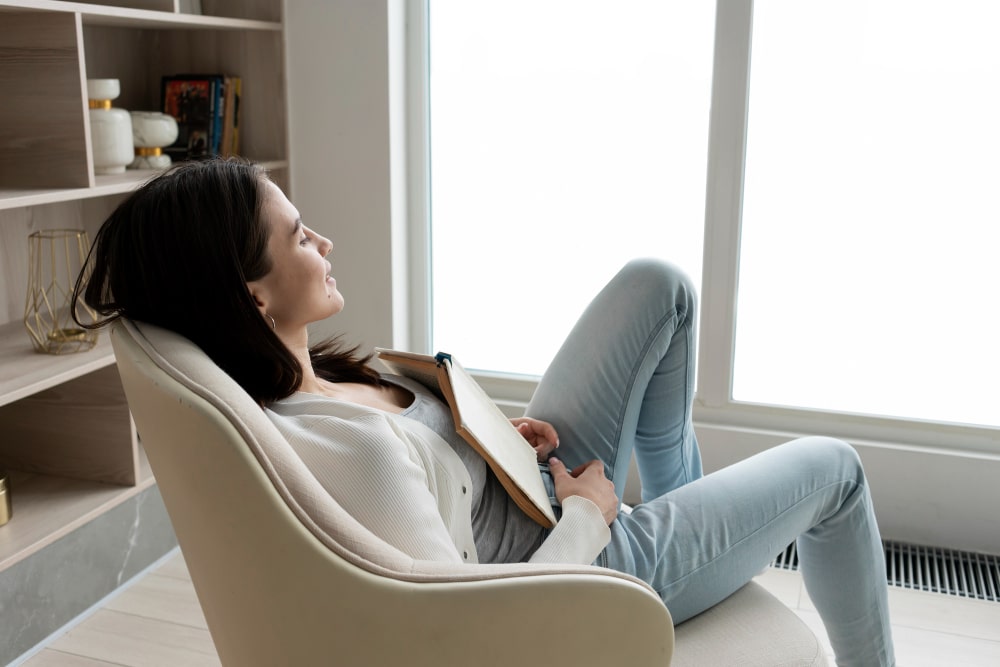
What is a Smart HVAC Controller?
A smart HVAC controller is an intelligent device that allows users to manage their HVAC systems remotely through smartphones or tablets. These energy-efficient HVAC devices, including heat pumps and ducted systems, can be integrated with air conditioners. By leveraging advanced algorithms and real-time sensor data, intelligent HVAC controllers optimise the performance of heating and cooling systems to maintain comfort while minimising energy consumption.
Key Functions
- Remote Monitoring and Control: Users can adjust settings from anywhere, ensuring optimal performance even when not on-site.
- Data Analytics: Many smart controllers provide insights into energy usage patterns, allowing for informed decision-making regarding energy consumption.
- Automation: They can adjust settings based on occupancy or time of day, increasing efficiency.
Benefits of Smart HVAC Controllers
Energy Savings
One of the core advantages of smart HVAC controllers is their ability to reduce energy consumption significantly. By optimising system performance through real-time adjustments to the right temperature based on occupancy and weather conditions, businesses can expect a reduction in energy bills ranging from 10% to 40%. In addition to reducing operating costs, this contributes to sustainability efforts by reducing carbon footprints.
Improved Indoor Air Conditioning
By using air quality sensors regulating temperature, humidity, and ventilation rates, smart HVAC controllers monitor air quality within buildings. These air conditioning systems contribute to better indoor environments by lowering allergens and pollutants by maintaining ideal conditions. Increased worker happiness and productivity can be attributed to better air quality.
Enhanced Comfort
With remote access capabilities, users can easily monitor and adjust temperature settings from their devices. This flexibility allows for personalised climate control that accommodates varying preferences among occupants. Scheduling features enable businesses and family members to set specific temperature profiles for different times of the day or week, ensuring comfort during working hours while saving energy during off-hours.
Increased Convenience
Integration with smart home systems adds another layer of convenience. Users can remotely control their HVAC systems alongside other smart devices through one app, single interface or voice commands via platforms like Amazon Alexa or Google Home. This interconnectedness simplifies management and enhances user experience.
Types of Smart HVAC Air Conditioning System Controllers
Understanding the different types of intelligent HVAC controllers available can help businesses choose the right solution for their needs:
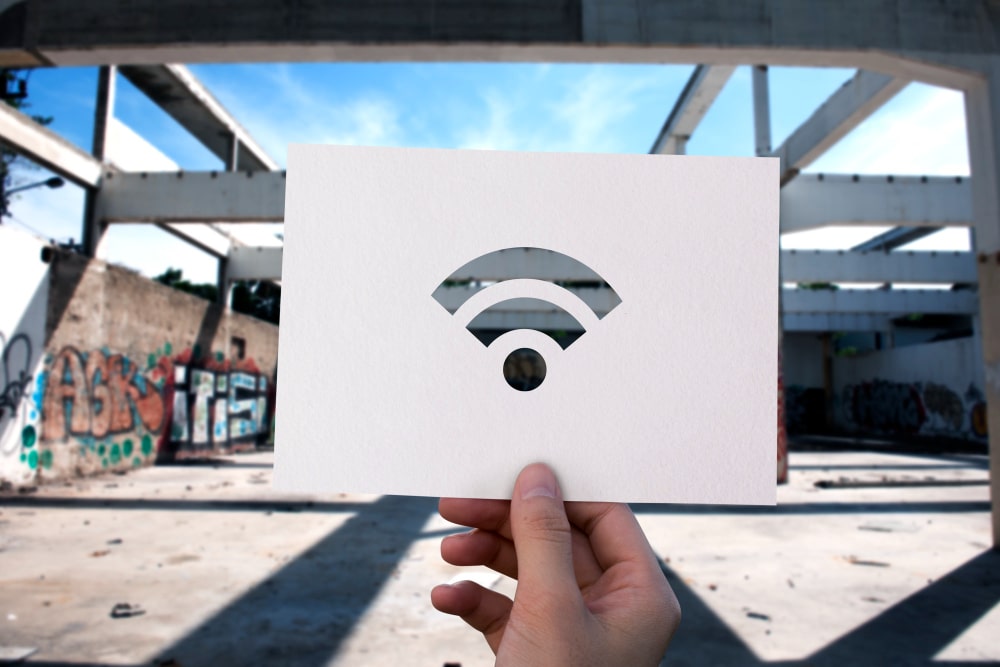
Wi-Fi Adapters
These devices can be retrofitted onto existing HVAC units to enable remote control capabilities without replacing the entire system. They serve as a bridge between traditional units and modern innovative technology.
Smart Thermostats
Smart thermostats are designed specifically for smartphones. They can be used to control temperature settings and schedule adjustments. They often come equipped with learning capabilities that adapt to user preferences over time.
Comprehensive Smart HVAC Systems
These systems integrate multiple climate control components into one cohesive unit, allowing for advanced heating, cooling, intelligent air conditioning, and ventilation management across large commercial spaces.
Features to Look for in a Smart HVAC Controller
When selecting an intelligent HVAC controller, consider the following essential features:
Remote Control Capabilities: Ensure the controller allows easy monitoring and adjustments via smartphones or tablets.
Scheduling and Automation: Look for features that enable users to set schedules based on occupancy patterns or specific times of day to optimise energy efficiency.
Air Quality Monitoring: Controllers with sensors that detect pollutants or humidity levels can automatically adjust settings to maintain healthy, sensible air quality.
Smart Home Integration: Compatibility with popular smart home platforms enhances convenience and allows for seamless control and management alongside other devices and accessories.
Versatility: Choose a controller that supports various HVAC systems to ensure compatibility with your house and existing infrastructure.
How Smart HVAC Controllers Work
Smart HVAC systems connect with HVAC systems using wireless technologies such as Wi-Fi or Zigbee. They gather data from various sensors, monitoring factors like temperature, humidity, room occupancy levels, and even external weather conditions to make real-time informed adjustments.
Programming and Automation
Users can program these controllers to operate under specific conditions; for example:
- Geofencing: The system detects when occupants leave or arrive at the building and adjusts temperature settings accordingly.
- Learning Algorithms: Some models learn user preferences over time and automatically adjust settings based on past behaviour.
Choosing the Right Smart HVAC Controller
Selecting the appropriate energy-efficient AC systems involves several considerations:
- Compatibility: Assess whether the controller is compatible with your existing HVAC system.
- Required Features: Based on your operational needs, determine which features are most important (e.g., air quality monitoring vs. essential temperature control).
- Energy Efficiency Potential: Research how different models perform regarding energy savings. Energy efficiency in HVAC systems helps you to avoid interruptions due to energy-related issues.
- User Reviews: Read reviews from other users to gauge reliability and performance.
- Cost vs. Value: Compare prices while considering long-term savings potential.
Installation and Setup
The installation process varies depending on the type of intelligent HVAC controller:
- DIY Options: Some controllers are designed for easy installation by users without professional help.
- Professional Installation: Hiring a professional may be necessary for more complex systems or integrations.
Always refer to manufacturer instructions during setup to ensure proper configuration.
Maintenance and Troubleshooting
To keep smart HVAC controllers functioning optimally:
- Regularly check and replace air filters or heat pumps.
- Update software and firmware periodically for security enhancements.
- Address common connectivity issues promptly by troubleshooting network connections or wifi adapters.
Energy Efficiency and Cost Savings
The financial benefits of implementing smart HVAC controllers are significant:
- Reduced Energy Consumption: By optimising system performance through automation and real-time adjustments.
- Lower Utility Bills: Businesses often see reductions in monthly energy expenses.
- Increased Asset Lifespan: Efficient operation reduces wear and tear, extending the lifespan of equipment and reducing replacement costs.
According to the U.S. Department of Energy, buildings with smart controls can achieve substantial energy savings without sacrificing comfort, making them an attractive investment for commercial property owners.
Smart Home Integration
Smart HVAC controllers can seamlessly integrate into broader smart home ecosystems:
- Compatibility with platforms like Amazon Alexa or Google Assistant allows users to control their systems through voice commands.
- Integration with other smart devices enables coordinated management—such as adjusting lighting based on temperature settings—enhancing overall building efficiency.
Remote Access and Control
For building managers, remote monitoring is a game-changer:
- Users receive alerts directly on their smartphones regarding system performance issues or maintenance needs.
- Remote access allows quick adjustments during off-hours or emergencies without needing physical presence on-site.
Final Thoughts
Smart HVAC controllers play a pivotal role in enhancing energy efficiency within commercial buildings by optimising climate control systems while improving comfort levels for occupants.
Their ability to provide total control, remote access, automation features, sensible air pro monitoring capabilities, and integration with smart home technologies make them invaluable tools in modern building management strategies.
Don't miss out on smart HVAC controllers' potential cost savings and convenience—consider implementing them in your commercial building today. For more information, contact us at 1300 740 140.
FAQs
What is smart HVAC control?
Smart HVAC, or intelligent climate control, refers to using technology, such as sensors and automation, to optimise the performance of building heating, ventilation, and air conditioning (HVAC) systems. This can include features like remote access, scheduling and automation, air quality monitoring, and integration with other smart home devices.
How much does a smart HVAC system cost?
The average cost to set up a new system would be about $10,000. Prices range considerably, from luxurious installations that cost up to $15,000 to more affordable choices that cost $5,000.
How can I make my HVAC smart?
You will need a compatible intelligent HVAC controller to make your smart HVAC control system smart. This device connects wirelessly to your existing HVAC system and enables it to be controlled through automation and remote access. Ensure that the controller is compatible with your current system before purchasing. Once installed, follow the manufacturer's instructions for setup and programming.
Can I make my ducted aircon smart?
Yes, you can make your ducted air conditioner a thoughtful air by installing a compatible Smart HVAC controller. This device will allow you to control your indoor unit and air conditioning system through automation and remote access.
Before purchasing, check the controller's compatibility with your specific ducted air conditioner model. Once installed, follow the manufacturer's instructions for setup and programming.
Read more
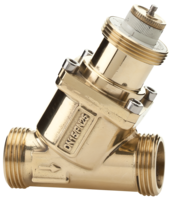
Balancing Acts: How PICVs Redefine Building Efficiency
Our sales team tend to field a lot of questions about control valves. Not surprising really, considering a fair chunk of our customers work in the building maintenance field. Most of these customers are looking for a direct drop-in to replace a tired old plug and seat valve, installed in a bygone era when TV was monochrome, and Elton John had hair (real hair).
But, just as Elton’s hair has moved on, so too has control valve technology. Enter stage right, the Pressure Independent Control Valve (PICV).
The Unsung Hero
Imagine stepping into a room where the air kisses your skin with the perfect hint of warmth or coolness - that's the artistry of the PICV at work. Think of it as your building's silent ninja, masterfully balancing the yin of energy consumption with the yang of thermal nirvana. These marvels of engineering are becoming the bedrock of modern buildings, where complexity is the norm, and energy efficiency is not just nice to have - it's a must-have.
The Inner Workings of a PICV
Understanding a PICV is like realizing your boring coworker is actually a wizard. A PICV merges two functionalities: flow regulation and differential pressure control.
Internals of a PICV. Credit: Siemens.
In a traditional system with fixed balancing valves, we're essentially playing a game of darts, where the board (the system pressure) is continuously moving. The PICV is that hustler who keeps hitting the bullseye.
When installed, the PICV is set to a desired flow rate. As water flows through the system, the valve measures the differential pressure across itself. If the pressure rises above the set point, the valve constricts, ensuring the flow rate remains consistent. Conversely, if the pressure drops, the valve opens wider to maintain the flow.
This dual action ensures that each part of a building receives the exact amount of heated or cooled water it needs, irrespective of changes in system pressure or demand from other parts of the building. It's the Goldilocks of building management: always keeping things just right. Ahhhh.
Temperature Control: It's Not Sexy, But It's Everything
Here's something you don't hear at cocktail parties: "Man, the PICV’s in my building are kicking ass." Why? Because nobody cares... until they're sitting in a pool of sweat or shivering like a Scottish nudist. A PICV, is the unsung hero in the shadows of our plantrooms, quietly balancing our comfort with the voracious energy appetite of modern buildings.
SmartX PIBCV. Credit: Schneider Electric
Saving Green by Going Green
PICVs aren't just about avoiding jumper weather indoors. They're about green - saving energy and cash. They slice through energy bills like a hot knife through butter, making building managers look like financial gurus and Mother Nature's BFFs.
Blueprints for the Future
The building game is changing. We're not just stacking bricks; we're crafting complex ecosystems. PICVs are the linchpins in this new world, where engineering marvel meets environmental stewardship. They're not just control valves; they're so much more than that.
Read more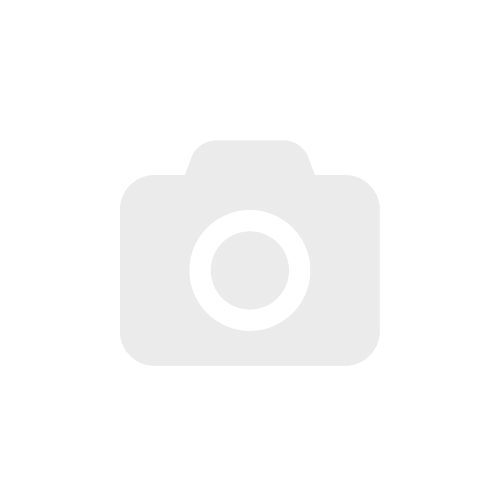
VEGA Guided Radar
This is a great product. Highly accurate and able to measure within very tight tolerances. Reach out to our team for more information!
Read more