What Are The Different Types of Actuators and Their Applications
Actuators are essential in industrial control systems, converting energy into mechanical motion. Their role in automation and energy conversion helps industries optimise performance, ensuring smoother, more efficient operations. Understanding actuator types aids engineers, facility managers, and manufacturing professionals in selecting the best solutions.
Understanding Different Types of Actuators – A Fundamental Overview
An actuator is a device that converts energy (electric, hydraulic, pneumatic) into mechanical motion. This energy transformation enables movement in systems that control industrial processes and automation. Actuators are responsible for executing commands within control systems, powering everything from robotic arms to valve operations.
Actuators receive input energy and convert it into an output motion. Depending on the actuator type, this motion can be linear or rotary. For instance, electrical energy powers electric actuators, while fluid pressure drives hydraulic actuators. Understanding these principles helps grasp their role in modern industry.
Linear vs. Rotary Actuators
Differences Between Linear and Rotary Actuators
- Linear Actuators: Produce straight-line motion. Common in conveyor systems, robotic arms, and industrial packaging, they enable precise, repeatable movement.
- Rotary Actuators: Generate circular motion and are vital for rotating machinery parts, automated valves, and assembly lines.
Examples in Industrial Applications
- Linear Actuators: Used in positioning and lifting mechanisms, as seen in assembly robots.
- Rotary Actuators: Essential for rotation processes, such as turning arms in production machinery.
Pneumatic Actuators – Speed and Efficiency
Structure and Characteristics of Pneumatic Actuators
Pneumatic actuators operate using compressed air, enabling fast and repetitive movements. They are known for their simplicity, high-speed operation, and low cost. These actuators are often lightweight and adaptable for various industrial tasks.
Applications
Pneumatic actuators excel in applications requiring rapid, cyclic operations, such as in packaging and bottling plants. Their efficiency makes them suitable for tasks where consistent movement is essential.
Hydraulic Actuators – Power and Precision
The Power of Hydraulic Actuators
Hydraulic actuators leverage fluid pressure to create motion, offering significant force output that is ideal for heavy-duty applications. Their precision and strength are unmatched, making them indispensable for heavy machinery tasks.
Industrial Use Cases
Hydraulic actuators are used in construction equipment like excavators and cranes, where substantial force and precision are needed to lift or move heavy loads. Their robust design ensures reliable operation under high-load conditions.
Electric Actuators – Precision and Control
Benefits of Electric Actuators
Electric actuators offer precise control and are generally low-maintenance. These actuators are powered by electric motors, which are ideal for tasks requiring exact movements and integration with digital control systems.
Practical Applications
Electric actuators are used in automated industrial processes where precision is a priority, such as robotics and conveyor systems. They also support smart systems through programmable controls, enhancing operational flexibility.
Comparing Actuator Types – Selection Guide
Actuator Comparison Table
|
|
|
|
|
|
|
|
|
|
|
|
|
|
|
|
|
|
|
|
Choosing the Right Actuator
Select an actuator by evaluating operational speed, force requirements, and environment. Pneumatic actuators suit high-speed, low-force tasks, while hydraulic ones are best for powerful, precise operations. Electric actuators are ideal for applications needing exact control.
Key Considerations When Choosing an Actuator
Critical Factors for Selection
- Load Capacity: Assess the force an actuator needs to handle.
- Operational Speed: Choose pneumatic for rapid cycles, hydraulic for power, and electric for controlled motion.
- Environment: Consider exposure to temperature extremes, moisture, or dust.
- Maintenance Expectations: Hydraulic actuators require more upkeep than electric or pneumatic options.
Real-World Applications of Different Actuators
Industrial Use Cases
- Pneumatic Actuators: Utilized in packaging machines where speed and repeatability are key.
- Hydraulic Actuators: Found in construction vehicles and presses due to their power capacity.
- Electric Actuators: Applied in robotic arms for precision assembly and automated adjustments.
Specific Industry Examples
- Manufacturing: Linear actuators in robotic welding.
- Construction: Hydraulic systems in cranes.
- Electronics: Electric actuators in automated testing machines.
Future Trends in Actuator Technology
Advancements Shaping the Industry
Integrating smart actuators and IoT is driving the future of industrial automation. These modern actuators offer enhanced data collection, enabling predictive maintenance and energy savings. The push for eco-friendly and energy-efficient actuators influences the shift towards electric models.
Energy Efficiency and Sustainability
Future trends indicate a move toward sustainable actuators that consume less energy and incorporate recyclable materials. Industries are increasingly adopting electric actuators because they are compatible with renewable energy sources and smart grids.
Conclusion
Actuators are pivotal for industrial processes due to their diverse types and capabilities. Understanding the benefits and limitations of pneumatic, hydraulic, and electric actuators helps select the most suitable solution for optimising operations.
Explore Controls Traders’ extensive range of actuators or contact their expert team for tailored advice in choosing the right actuator for your needs.
FAQs
What is the best type of actuator for high-speed operations?
Pneumatic actuators are ideal due to their rapid movement and cost-effectiveness.
How do hydraulic actuators compare to electric actuators in terms of maintenance?
Hydraulic actuators require more maintenance due to fluid handling and potential leaks, whereas electric actuators are low maintenance and reliable.
Are electric actuators cost-effective for long-term use?
Yes, despite higher initial costs, electric actuators offer long-term savings in energy and maintenance.
Can I use actuators in harsh outdoor environments?
Hydraulic actuators perform well in rugged conditions, while pneumatic actuators are robust but require dry air to avoid corrosion.
What are the most common applications for linear actuators?
Due to their precise linear motion, linear actuators, such as conveyor lines and robotic arms, are essential in automation systems.
Leave a comment
Popular Posts
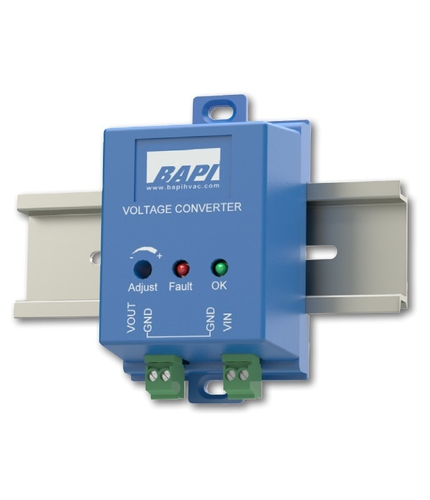
Voltage Converters: Learn How They Work and How to Pick the Best Type
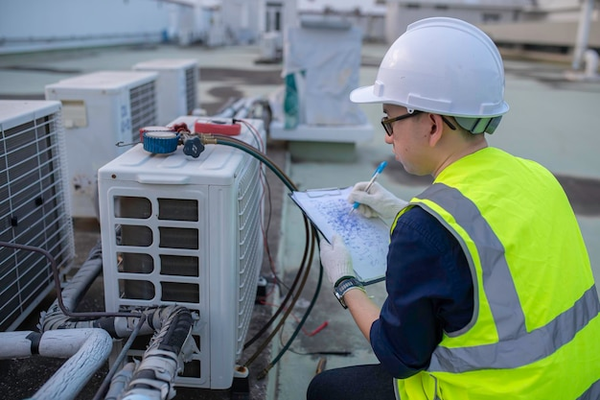
What is a Variable Speed Drive? A Beginner’s Guide to Understanding VSDs
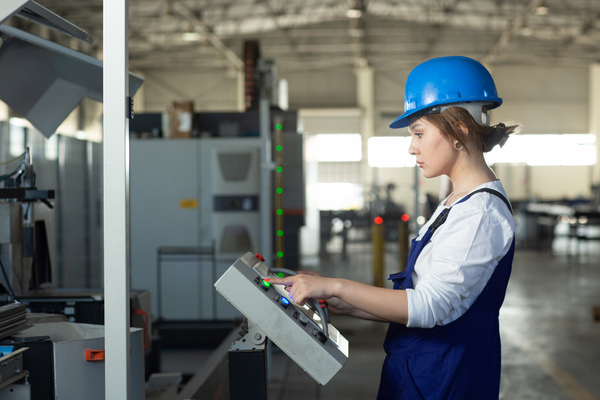
What is a VFD in HVAC and How Does it Work?
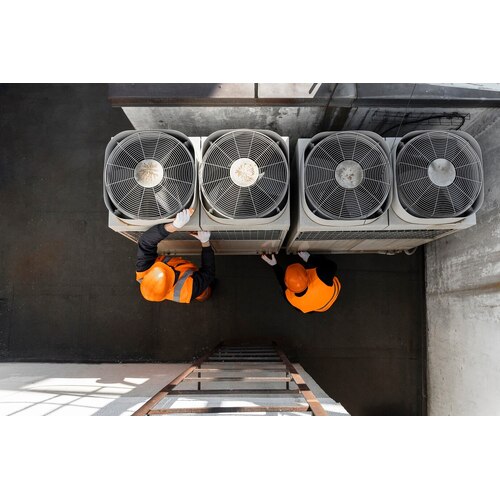