HMI or Human Machine Interface: A Comprehensive Guide
Human Machine Interface (HMI) has become a cornerstone of modern industrial control systems. By serving as the communication bridge between operators and machinery, HMIs enhance productivity, safety, and operational efficiency. According to Controls Traders, known for its innovative solutions in industrial technologies, HMI panels play a vital role in fostering safe, reliable, and effective work environments.
What is HMI? Definition and Core Applications
So, what does HMI mean? Human-machine interface (HMI) is the technology that facilitates interaction between humans and machines, providing a user-friendly platform for monitoring and controlling industrial processes. According to industry experts, HMI screens empower operators to manage operations effectively, from straightforward tasks to complex automation.
Core Applications:
- Manufacturing: HMI panels provide real-time data and control for production line management, ensuring operational efficiency and reduced downtime.
- Energy Sector: HMI displays are essential for grid management and energy distribution monitoring, supporting a stable and reliable energy flow.
- Logistics: Human Machine Interfaces automate warehouse operations and enhance inventory management through accurate tracking and visualisation.
Common HMI tools include touch panels, graphical user interfaces (GUIs), and integrated HMI displays that interface with PLCs (Programmable Logic Controllers) and other industrial control units.
The Evolution of HMI Technology
HMI technology has significantly evolved, shifting from basic mechanical controls to advanced touch-based and AI-integrated systems. According to Tech Trends Journal, early control systems in the 20th century relied on mechanical switches and indicator lights for basic operations. The introduction of text-based terminals in the 1980s began the shift towards more interactive systems, allowing limited operator interactions.
Key Milestones:
- 1980s: The introduction of text-based terminals began the era of limited interactive HMI screens.
- 1990s-2000s: The emergence of graphical touchscreens revolutionised the field, enabling more complex and visually driven interactions.
- Present Day: HMIs now incorporate AI and cloud technology, offering adaptive, remote-capable, and predictive interfaces that align with digital transformation trends.
Key Features and Benefits of Modern HMI Systems
Modern HMI systems featuring advanced HMI design, enhance operational control and efficiency.
Key Features:
- Real-time Data Visualisation: Operators can see and respond to data instantly, allowing for informed decision-making.
- Custom Interfaces: Flexible layouts tailored to specific processes and operational needs.
- User Accessibility: Intuitive HMI panel for easy navigation and quick onboarding.
- Adaptive Layouts: Configurable displays that evolve with process requirements.
Benefits:
- Enhanced Safety: Integrated safety alarms and alerts notify operators of system anomalies.
- Operational Efficiency: Simplifies complex processes and allows for rapid response to issues.
- Data Analytics Tools: Facilitates predictive maintenance by identifying performance patterns.
- Remote Monitoring: Ensures continuous oversight through remote access, supporting varied operational scenarios.
Applications of HMI in Different Industries
The adaptability of HMI systems allows for their use across various industries, enhancing process optimisation and reducing downtime.
Industry Examples:
- Manufacturing Plants: Real-time HMI displays help monitor production lines, enabling quick adjustments to prevent bottlenecks and delays.
- Energy Facilities: Operators use HMI screens to monitor and control energy outputs, maintaining consistent and reliable distribution.
- Logistics Centres: HMI panels with dashboards track inventory and coordinate vehicle movement, reducing errors and enhancing throughput.
According to a study published by Industry Solutions Weekly, companies using HMI dashboards have significantly improved operational transparency and reduced system failures.
Best Practices for HMI Design and Implementation
The effectiveness of HMI systems largely depends on user-focused HMI design and careful implementation.
Guidelines:
- User Experience (UX) Design Priority: Ensure intuitive and straightforward interfaces.
- Customisation Options: Adaptable configurations to meet specific operational needs.
- Training and Education: Comprehensive training programs maximise system potential.
- Software Compatibility: Seamless integration of HMI software with existing control systems.
- Feedback and Iteration: Regular user feedback to refine the interface.
Challenges and Future Prospects of HMI Technology
Despite many advantages, HMI technology faces challenges and holds promising prospects for the future.
Current Challenges:
- Cybersecurity Risks: Data security must be ensured as HMIs connect to larger networks.
- Legacy System Integration: Compatibility issues with older equipment.
- Complexity in Design: Balancing feature-rich interfaces with user-friendliness.
Future Trends:
- AI-Enhanced Interfaces: Machine learning will drive predictive functions and smarter decision-making.
- Augmented Reality (AR): AR could provide enhanced training and maintenance directly through HMI displays.
- Cloud Connectivity: Expanded cloud-based capabilities for real-time remote access.
The future of HMI points towards smarter, more connected systems that seamlessly integrate with cloud and augmented technologies, promoting productivity and connectivity.
Conclusion
HMI technology has become critical in modern industries, offering real-time control, increased safety, and greater process efficiency. Adopting advanced HMI solutions is essential for companies seeking operational excellence and competitive advantage. As industries progress towards higher levels of automation, embracing cutting-edge HMI technologies positions organisations to optimise their workflows, reduce downtime, and enhance overall productivity.
Explore how Controls Traders can support your HMI needs with expert solutions tailored for the industrial sector. Visit Controls Traders to discover premium HMI products and services that elevate your operations with reliability and innovation. Connect with our team to find the right HMI solution for your business.
FAQs
What does HMI stand for in industrial automation?
HMI stands for Human Machine Interface, facilitating communication between humans and machines.
How does an HMI differ from a PLC?
An HMI is an interactive user interface, while a PLC is an automated system for executing control functions.
What are the key benefits of using HMI in industrial processes?
Improved safety, real-time data access, and streamlined process management.
What challenges exist when implementing HMI technology?
Challenges include cybersecurity, legacy system integration, and design complexity.
What future trends can we expect in HMI technology?
AI-driven enhancements, augmented reality, and cloud-based solutions.
Leave a comment
Popular Posts
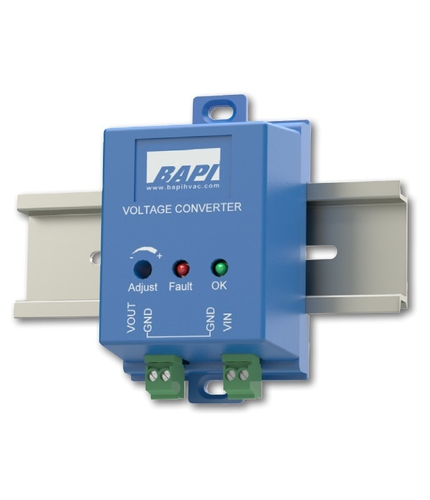
Voltage Converters: Learn How They Work and How to Pick the Best Type
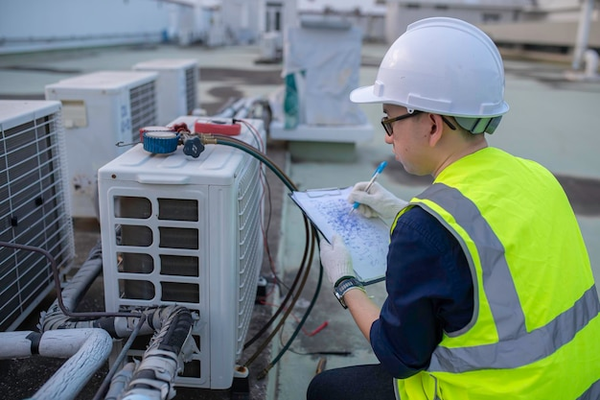
What is a Variable Speed Drive? A Beginner’s Guide to Understanding VSDs
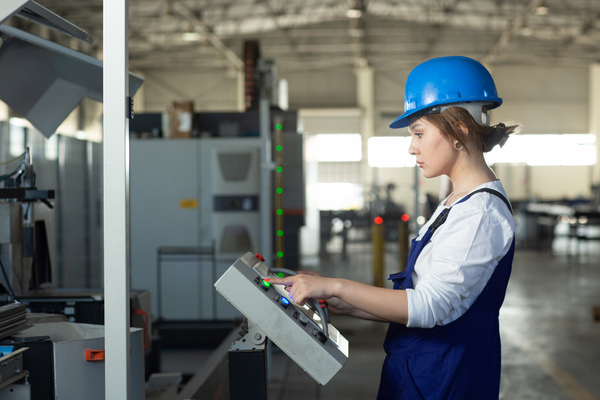
What is a VFD in HVAC and How Does it Work?
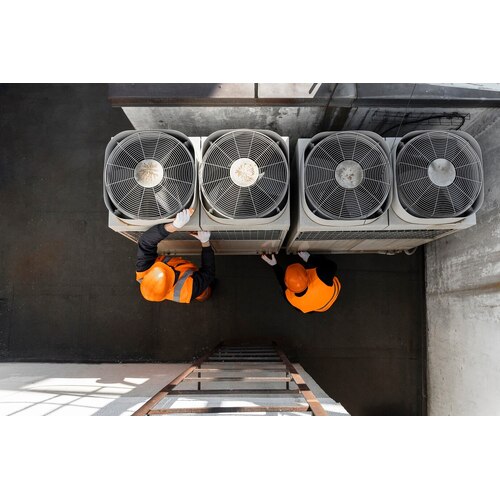