Pressure Switch: Functionality, Types, Applications, Calibration and Safety Features
Understanding the multifaceted role of pressure switches is critical for industries reliant on precise pressure management. These devices, integral to systems ranging from water pumps to air compressors, operate by activating or deactivating circuits in response to pressure changes. The diversity of pressure switches—mechanical, electronic, and differential—ensures suitability across varied applications. Accurate calibration, achieved through specialised tools, is paramount for maintaining operational reliability. Additionally, safety features like interlocks and pressure cutout mechanisms are imperative to prevent failures. To comprehend their full impact and functionality, one must explore their types, applications, and safety protocols in greater detail.
What is a Pressure Switch?
According to Controls Traders, a pressure switch is an electrical device designed to monitor and respond to changes in pressure within a system. It operates by detecting when the pressure reaches a predefined threshold and then activating or deactivating a circuit.
There are two main types: mechanical pressure switches and electronic pressure switches. Mechanical switches use physical mechanisms, while electronic switches utilise pressure sensors.
These devices can monitor various pressure types, such as air pressure and differential pressure. Pressure setting ranges determine the specific pressures at which the switch operates.
Proper pressure calibration guarantees accuracy and reliability. Safety features are integral, preventing system failures and guaranteeing operational efficiency.
Pressure switches are essential in maintaining system integrity and performance in numerous applications.
How Does a Pressure Switch Work?
Understanding the inner workings of a pressure switch involves examining its key components and the mechanisms they utilise to detect and respond to pressure changes. A pressure switch typically consists of a sensor that measures pressure, an electromechanical mechanism to convert pressure changes into electrical signals, and an adjustment range to set specific pressure thresholds.
When the sensed pressure reaches a pre-set level, the switch activates or deactivates an electrical circuit. Calibration guarantees accurate functionality and is essential for maintaining safety features across various applications.
Differential pressure switches operate on similar principles but measure the difference between two pressure points. Their reliability and precision make them indispensable in many industrial and commercial settings.
What are the Types of Pressure Switches?
Several distinct types of pressure switches cater to various industrial and commercial needs.
Mechanical pressure switches operate using a diaphragm or piston mechanism to detect pressure changes.
Electronic pressure switches utilise sensors and digital interfaces for more precise control and monitoring.
Differential pressure switches measure the difference between two pressure points, ensuring accurate readings across a specified pressure range.
Each type has unique calibration requirements and safety features tailored to their specific applications.
Mechanical switches are often preferred for their simplicity, while electronic options offer advanced switching functions and higher precision.
Understanding these types is essential for selecting the right pressure switch for your system's needs and ensuring peak performance and safety.
What Materials are Used in Pressure Switches?
Pressure switches are constructed from various materials to guarantee durability, reliability, and compatibility with different environments and media.
Stainless steel and brass are commonly used for components in contact with media, known as the wetted area, due to their corrosion resistance and strength.
Diaphragms within pressure switches often utilise flexible materials like rubber or metal to detect changes in hydraulic pressure or air pressure switches.
Sensors and pressure transducers are typically made from robust materials to withstand harsh environments.
Electrical contacts, essential for signal transmission, are often crafted from conductive metals.
The choice of materials guarantees the pressure switch performs reliably under varying conditions and extends its operational lifespan.
What are the Physical Dimensions of a Pressure Switch?
When considering the physical dimensions of a pressure switch, it is vital to recognise that these devices can vary considerably in size depending on their specific application and design requirements.
Pressure switches can range from compact designs for limited space applications to larger models suitable for high-pressure capacities.
The physical dimensions are influenced by the type of pressure sensor, safety features, and the inclusion of an adjustment screw for calibration.
Different types of pressure switches cater to various applications, each with unique space constraints and functional demands.
Understanding the physical dimensions is essential for proper installation and ensuring that the pressure switch meets the specific needs of the system it is integrated with.
How to Install a Pressure Switch?
Installing a pressure switch involves gathering the necessary tools and following a series of methodical steps.
Essential tools typically include wrenches, screwdrivers, and a pressure gauge.
The installation process encompasses mounting the switch, connecting wiring, and calibrating the device to guarantee proper functionality.
What Tools are Needed to Install a Pressure Switch?
To install a pressure switch, a specific set of tools is required to guarantee proper functionality and safety.
Essential installation tools include a pressure gauge to monitor system pressure, a control valve for flow regulation, and a pressure regulator to maintain desired pressure levels.
Additionally, tools for connecting to the electrical circuit are necessary, such as wire strippers and screwdrivers.
For systems involving water pressure, float switches may be required. An air compressor can aid in pressurising the system for testing purposes.
Adhering to safety features is vital; hence, personal protective equipment (PPE) like gloves and safety glasses should be used.
Proper tools assure the pressure switch operates effectively and maintains system integrity.
What are the Steps to Install a Pressure Switch?
Proper installation of a pressure switch involves several systematic steps to guarantee reliable operation and system safety.
Start by ensuring the system is de-energised to meet safety features.
Identify the correct location for the pressure switch installation near the inlet pressure source.
Connect the pressure switch to the pneumatic or fluid pressure line, ensuring all fittings are secure.
Adjust the pressure settings according to system requirements.
Use a calibration device to verify accuracy.
Connect the electromechanical control pressure switch to the electrical system, following wiring diagrams.
Power up the system and test the pressure switch to confirm it responds correctly to changes in pressure.
What are Common Applications of Pressure Switches?
Pressure switches are commonly used in a variety of industrial, commercial, and residential applications to monitor and control pressure levels.
In water pumps, they guarantee proper pressure and prevent damage due to overpressure. Air suspension systems in vehicles utilise pressure switches to maintain ideal ride quality. Compressors use them to regulate air pressure and avoid system failures. In flow control, they help manage fluid dynamics in pipelines. Wastewater treatment facilities use pressure switches to maintain safe and efficient operations.
These devices are integral to automation control products, providing essential feedback and enabling automated responses. Safety features and precise calibration are critical in all these applications to guarantee reliability and performance.
How to Calibrate a Pressure Switch?
Calibrating a pressure switch requires specific equipment such as a pressure source, a calibrated pressure gauge, and adjustment tools.
The process involves setting the switch to the desired pressure range and fine-tuning the set points to guarantee accurate operation.
Following a systematic approach, involving precise steps, assures the switch functions reliably within its designated parameters.
What Equipment is Needed to Calibrate a Pressure Switch?
To calibrate a pressure switch, specific equipment such as a pressure source, a reference gauge, and a calibration device is essential. The pressure source provides the necessary psi for testing.
Pressure gauges and sensors guarantee precise pressure management by displaying accurate measurement values. Transducers convert pressure into an electrical signal that can be read by the calibration device.
This device compares the pressure switch's response to the known reference values, affirming its accuracy. Adjustable pressure settings on the calibration device allow for fine-tuning to match the desired operational parameters.
Proper calibration guarantees reliable performance, contributing to the overall safety and efficiency of any system using pressure switches.
What are the Steps to Calibrate a Pressure Switch?
Effective calibration of a pressure switch involves several methodical steps to ascertain accurate and reliable operation.
Begin by isolating the pressure switch from the system to guarantee safety. Connect a calibrated pressure source to the switch. Gradually apply mechanical pressure or electronic pressure until the switch point is reached.
Adjust the switch to the desired preset pressure level. Next, reduce the pressure to determine the reset point. Measure and record hysteresis, the difference between the switch point and reset point.
Make necessary adjustments to achieve peak performance. Repeat the process to confirm accuracy. Proper calibration enhances service life and guarantees reliable water pressure control.
Always follow manufacturer guidelines and use precise instruments for best results.
What are the Safety Features of a Pressure Switch?
A pressure switch incorporates several safety features designed to prevent system failures and guarantee reliable operation.
High pressure and low pressure switches are equipped with interlocks to protect equipment by shutting down systems when pressure levels exceed safe limits.
Pressure cutout mechanisms are essential for preventing over-pressurisation, which could lead to hazardous conditions.
In explosion-hazard environments, pressure switches are designed to minimise the risk of triggering explosions.
Additionally, maintaining consistent water pressure and managing pressure differentials are critical safety features that maintain system stability.
These features collectively enhance the reliability and safety of pressure switches across various applications, making them indispensable for maintaining operational integrity and preventing potential damage or accidents.
How to Troubleshoot a Pressure Switch?
When troubleshooting a pressure switch, it is essential to first identify common issues such as incorrect pressure settings, electrical faults, or mechanical wear.
Understanding the latest innovations in pressure switch technology, including digital interfaces and advanced diagnostics, can aid in more effective problem-solving.
Additionally, new materials like corrosion-resistant alloys and high-performance polymers enhance durability and reliability.
What are Common Issues with Pressure Switches?
Common issues with pressure switches often stem from improper calibration, electrical problems, or mechanical failures.
Calibration errors can lead to inaccurate pressure readings, affecting the performance of the pressure switch and associated systems.
Electrical problems, such as faulty wiring or loose connections, can disrupt the signal transmission between the pressure switch and control unit.
Mechanical failures, like worn-out diaphragms or clogged pressure ports, can prevent the pressure switch from operating correctly.
Pressure spikes and pump damage can occur if the sensor type electromechanical pressure switch fails to provide adequate protection on water pumps.
Regular maintenance and calibration are essential to guarantee the safety features and applications of pressure switches function effectively, mitigating common issues and maintaining system integrity.
What are the Latest Innovations in Pressure Switch Technology?
Advancements in pressure switch technology have led to the development of more accurate, reliable, and versatile devices suitable for a wide range of applications.
Among the latest innovations are digital displays and multicolour switching displays, enhancing functionality and user interface.
Modern electromechanical pressure switches now offer improved calibration features, guaranteeing precision and consistency.
These innovations enable more efficient monitoring and control in various types of applications, from industrial automation to HVAC systems.
Enhanced safety features have also been integrated, providing better protection against overpressure conditions.
These technological advancements guarantee that pressure switches remain indispensable tools for maintaining operational safety and efficiency.
What New Materials are Being Used in Pressure Switches?
Recent developments in material science have introduced advanced composites and high-performance alloys into the construction of pressure switches, greatly enhancing their durability and functionality.
These new materials improve the performance of components and sensors under extreme temperature conditions, making them ideal for specialist industry applications. Enhanced materials also contribute to more accurate calibration, resulting in better reliability and safety features.
In demanding environments, such as chemical processing or oil and gas extraction, these pressure switches exhibit resilience and precision, ensuring peak performance.
The integration of these advanced materials into pressure switch design reflects a significant step forward in meeting the rigorous demands of modern applications, ultimately broadening their scope of use and effectiveness.
Leave a comment
Popular Posts
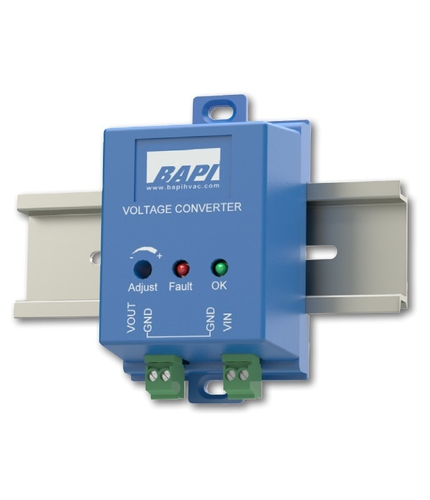
Voltage Converters: Learn How They Work and How to Pick the Best Type
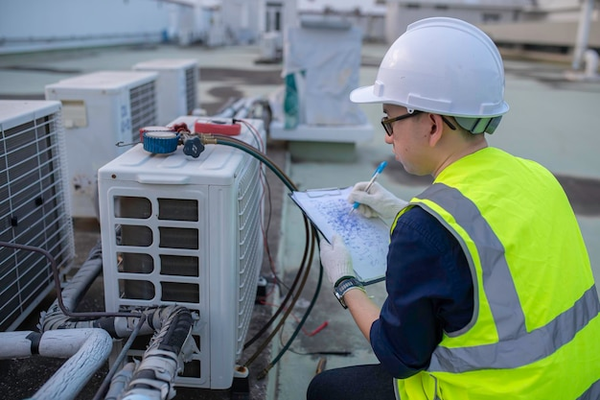
What is a Variable Speed Drive? A Beginner’s Guide to Understanding VSDs
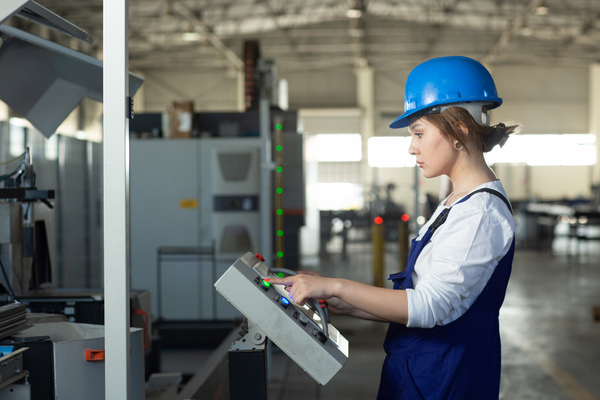
What is a VFD in HVAC and How Does it Work?
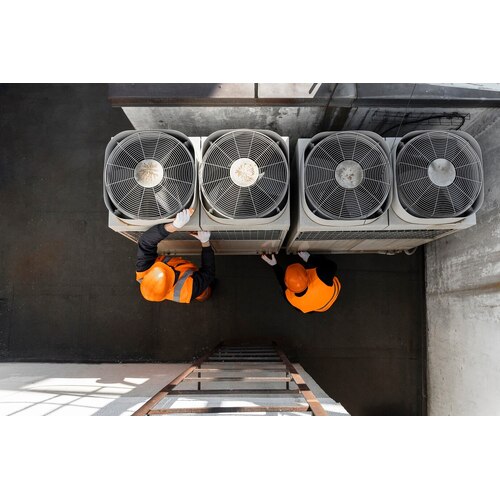