What is a VFD in HVAC and How Does it Work?
Have you ever noticed how your air conditioner blasts cold air at full-speed, even when it’s only mildly warm? That’s energy down the drain. Now, imagine if it could adjust itself, slowing down when needed, speeding up when necessary. That’s exactly what a Variable Frequency Drive (VFD) does in an HVAC system, often working alongside precision instruments from WIKA for accurate monitoring and control.
A VFD is a motor controller that regulates the speed of an electric motor by varying its frequency and voltage. Instead of running at full speed all the time, the motors only work as hard as they need to. That means lower energy consumption, less wear and tear, and better system performance. Let’s unpack it a bit more.
VFD Meaning: What Does VFD Stand For?
VFD stands for Variable Frequency Drive. It’s sometimes called an AC drive or adjustable speed drive, but the idea is the same. It controls how fast a motor spins.
So, how does it do that? A VFD tweaks both the frequency and voltage of the electricity going to a motor. The lower the frequency, the slower the motor. The higher it is, the faster it runs.
Now, you might’ve heard of a Variable Speed Drive (VSD) and wondered, “Isn’t that the same thing?” Not quite. A VSD refers to any device that changes a motor’s speed, while a VFD specifically does it by adjusting frequency and voltage.
Think of it like this—every VFD is a VSD, but not every VSD is a VFD. It’s like how all squares are rectangles, but not all rectangles are squares.
Now, let’s go into how a VFD actually works.
How Does a VFD Work in HVAC?
Controlling Motor Speed with Frequency and Voltage
Have you ever left a tap running full blast when you only needed a trickle? That’s what happens when an HVAC system runs at full speed all the time. It wastes energy.
A Variable Frequency Drive (VFD) fixes this by adjusting motor speed to what's needed. It changes the frequency and voltage of the electricity supplied to the electric motor, letting it speed up or slow down as needed.
When demand is low, the motor slows down, using less power. When more airflow or cooling is needed, it speeds up. This speed control cuts energy consumption, improves efficiency, and reduces wear on equipment. In fact, HVAC systems with VFDs can slash energy use by up to 50%, which is great for both the environment and your power bill.
Key Components of a Variable Frequency Drive (VFD)
A VFD isn’t just a black box that magically saves energy. It has four key parts working together to control motor speed:
- Rectifier: Converts AC power into DC voltage.
- DC Bus: Stores and smooths the DC voltage, ensuring steady power.
- Inverter: Converts DC back to AC using pulse width modulation (PWM), controlling the output voltage.
- Control Unit: The brains of the operation. It adjusts the frequency and voltage, managing motor speed and response.
Together, these components make sure the electric motor runs only as hard as it needs to—no more, no less.
Why Use a Variable Frequency Drive (VFD) in HVAC Systems?
Think about an office building on a mild spring day. The aircon doesn’t need to work as hard, but without a VFD, it still runs like it’s the middle of summer, which is wasteful, right?
With a variable frequency drive, the system slows down when cooling demand drops and ramps up when needed. That means better efficiency, lower costs, and longer-lasting equipment.
Energy Savings and Efficiency
HVAC systems consume a massive chunk of a building’s electricity, up to 70% in some cases. Running them at full speed all day is like driving a car with your foot flat on the accelerator, even when you're in traffic.
A variable frequency drive (VFD) solves this by adjusting motor speed to match demand. Less power wasted means lower energy bills. In commercial buildings, VFDs can cut electricity costs by 30% to 50%, which adds up fast.
Reducing Equipment Wear and Enhancing Performance
Have you ever heard an old aircon unit rattle and shake when it kicks on? That’s the strain of starting at full power. It wears down components and leads to breakdowns.
With a VFD, motors start up gradually, reducing stress on motor windings and driven equipment. That means less maintenance, fewer breakdowns, and a longer lifespan for HVAC systems.
It’s simple: less strain, fewer repairs, more savings. That’s why we recommend that VFDs be used in modern HVAC systems.
Choosing the Right Variable Speed Drive (VSD) for HVAC
Picking the right variable speed drive (VSD) for your HVAC system isn’t just about power. It’s about efficiency, longevity, and cost savings. Get it wrong, and you could be dealing with overheating motors, higher energy bills, or unnecessary breakdowns. So, how do you choose the best one?
Sizing and Selection Guide for Variable Frequency Drives
Size matters, especially with variable frequency drives (VFDs). Choose wrong, and you’re either overloading your system or wasting money on an oversized unit. Here’s what to consider:
- Motor Power: Your VFD must match the motor load. Check kW ratings and ensure the drive isn’t underpowered.
- Voltage Levels: In Australia, HVAC motors typically run at 230V single-phase or 415V three-phase. So, get a VFD with the right input and output voltage.
- Load Type: HVAC systems usually require a variable torque drive. That means your VFD needs a capacity to control ramp speeds efficiently.
For example, in a commercial building, a VFD running an AC induction motor might need pulse width modulation (PWM) for smoother operation. No one wants a jerky airflow system.
Installation and Maintenance Best Practices
Installing a variable frequency drive VFD is not rocket science, but get it wrong, and you’ll be calling an electrician more often than you’d like.
Here’s how to get it right:
- Proper Wiring: Connect it correctly to the power supply and motor windings. Use shielded cables to avoid interference.
- Cooling & Ventilation: VFDs generate heat. Keep them in a well-ventilated space to prevent overheating.
- Routine Checks: Dust and debris can clog vents. A quick monthly clean helps save energy and improve lifespan.
- Monitor Performance: Use built-in diagnostics to fine-tune system performance. Adjusting motor speed can slash power costs.
Note: A well-maintained variable frequency drive can last 10+ years, keeping your HVAC system running efficiently.
Best HVAC Variable Frequency Drive (VFD) Brands
Not all VFDs are the same. Some last longer, run smoother, and offer better energy savings. Here are the top brands trusted in Australia:
- Siemens: Siemens is known for energy savings and intelligent motor control. Great for large-scale HVAC systems.
- Danfoss: Danfoss is the leader in HVAC VFDs. Their VLT and Vacon drives are found in many Aussie buildings.
- ABB: Reliable and built for medium voltage AC drives. Ideal for high-performance applications.
- Schneider Electric: Easy to use, with built-in protection against power surges. A solid mid-range option.
Need a reliable VFD or AC drive for your HVAC system? Check out Controls Traders in Adelaide. We stock high-quality drives from Danfoss to Siemens and more.
Final Thoughts
A variable frequency drive does more than just control motor speed. It reduces energy consumption, extends motor life, and keeps your HVAC system running smoothly.
Choosing the right VFD means fewer breakdowns, lower power bills, and a more comfortable space. So whether you’re managing an office, shopping centre, or industrial plant, a well-sized variable speed drive is a smart investment.
Need help finding the best VFD? You can shop for them here at Controls Traders on our dedicated store for variable speed drives.
Frequently Asked Questions
What are the three types of VFD?
There are three main types of variable frequency drives (VFDs)—Voltage Source Inverter (VSI), Current Source Inverter (CSI), and Pulse Width Modulation (PWM). VSI is the most common and works well for HVAC systems. CSI is used in heavy-duty industrial settings, while PWM provides the smoothest speed control, reducing noise and making motors run more efficiently.
What is the difference between a PLC and a VFD?
A Programmable Logic Controller (PLC) is like the brains of an operation, while a VFD is the muscle. A PLC manages different system processes, like turning fans on and off or adjusting airflow. A VFD is a type of AC drive that controls the speed of the motor, making sure it runs at just the right level instead of wasting energy.
Is a VFD used in AC or DC?
A VFD is made for AC motors, especially AC induction motors. It takes incoming AC power, converts it to DC voltage, then turns it back into AC power at different frequency and voltage levels. This lets the system fine-tune motor speed, helping save energy and extend the life of the equipment.
What is the difference between an inverter and a VFD?
An inverter changes DC power into AC power, like what you’d see in solar or backup battery systems. A VFD, on the other hand, is a type of motor controller that drives an electric motor by tweaking frequency and voltage. This means a VFD doesn’t just convert power—it actively controls how fast a motor runs, making it perfect for HVAC and industrial systems.
How do frequency and voltage affect motor speed in a VFD system?
In a VFD system, frequency and voltage work together to set the speed of the motor. More frequency and voltage means faster speed. Less means slower. This speed control is what makes variable frequency drives so useful—they adjust power based on demand, cutting down on energy consumption and preventing unnecessary wear and tear.
Got more questions or need help choosing a VFD? Send us a message or call us at 1300 740 140
Leave a comment
Popular Posts
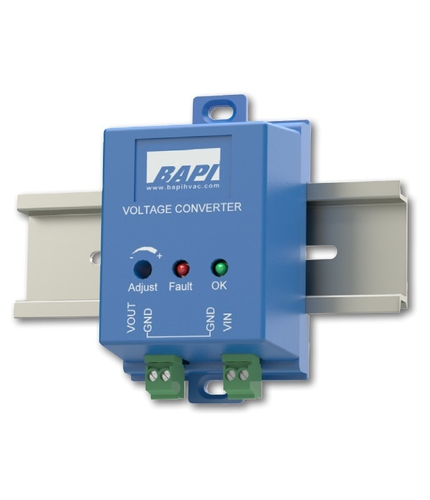
Voltage Converters: Learn How They Work and How to Pick the Best Type
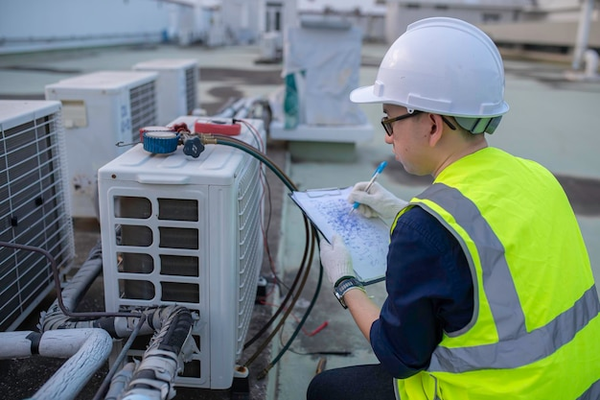
What is a Variable Speed Drive? A Beginner’s Guide to Understanding VSDs
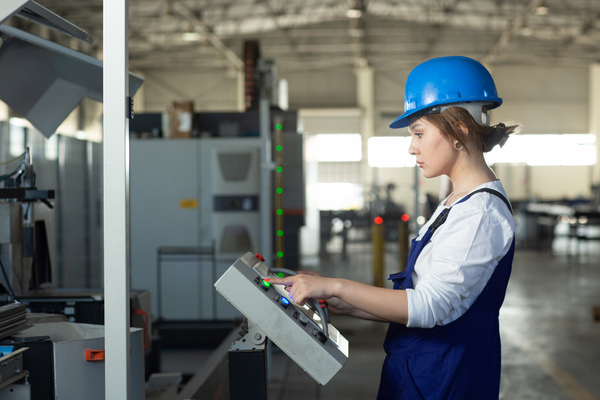
What is a VFD in HVAC and How Does it Work?
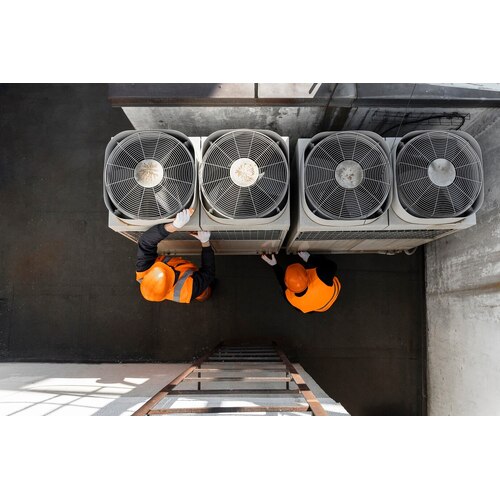